Progressive Die Stamping vs. Transfer Die Stamping: Comparison Guide
The different types of die stamping used in modern day manufacturing are constantly evolving. From the techniques they use, to their efficiency, to the industries they serve, it’s important to keep up to date on the advancements of methods leading the manufacturing sector today.
Two popular metal stamping methods are progressive die stamping and transfer die stamping.
In this article, we’ll walk through the progressive die versus transfer die stamping processes, including their key differences and how those differences impact their overall suitability for certain parts and designs.
What is Progressive Die vs. Transfer Die Stamping?
We’ll start with the basics of progressive die and transfer die stamping.
Progressive Die Stamping
The progressive die stamping process involves a press containing several stations with a single die, each performing a different operation (cutting, shaping, embossing, etc.) on a part on a single, continuous run. Progressive die stamping combines several different operations in one process, helping reduce overall production times. The process is efficient and cost-effective for large-quantity production.
Transfer Die Stamping
This process involves one or multiple stations each with their own individual dies performing a different action on the piece. A metal strip isn’t required – an initial shape is cut, and the part must then be mechanically or manually transferred to the next station(s). This process is often used for larger, complex, highly customized shapes that benefit from individual stations performing precise operations at different angles. The process is slower and more expensive than progressive stamping, but still highly precise.
Resource: Intro to Die Stamping Tools
Key Differences Between Progressive Die and Transfer Die Stamping
You can already see some of the key differences between progressive die and transfer die stamping – including the process the part undergoes and the tools used. Here’s a chart providing an overview of each method. Then, we’ll dive deeper into each distinction below.
|
|
|
What is it? |
A metal stamping process where a part is passed through multiple stations on a single run to create the desired part |
A metal stamping process where a part is passed through several stations on several individual runs to create the desired part |
How many dies does it use? |
Single die performing multiple different techniques |
Multiple dies each performing a different, single technique |
How does the part move from station to station? |
Single run |
Multiple runs |
What types of stamping are applicable? |
Bending, cutting, drawing, embossing, lancing, punching, coining, extruding, etc. |
Exclusive techniques like adding ribs, threading, cutouts, holes, knurls |
What projects is it best suited for? |
High-volume quantities |
Large, complex parts |
How much does it typically cost? |
Lower operational costs, higher upfront cost of machinery |
Higher operational costs |
1. Progressive Stamping is More Efficient than Transfer Stamping
In progressive die stamping, the part passes through a single machine with a single die, moving through multiple stations on a single, continuous run until completion. Since it only goes through one run, it reduces manufacturing lead times, making it one of the more efficient methods, especially when compared to transfer die stamping.
In transfer die stamping, a part is moved manually or mechanically through a machine with one or more distinct stations on several runs. Unsurprisingly, the transfer of parts from station to station and the complex design stamping makes it more time-consuming than progressive die stamping.
2. Transfer Stamping uses Multiple Dies while Progressive Stamping uses One
Progressive die stamping uses a single die to complete a number of different stamping techniques. Some stamping techniques used in progressive stamping include bending, cutting, lancing, embossing, and punching, amongst others. The ability to complete multiple techniques at fast rates with one die makes it an ideal stamping choice for parts with simpler designs at higher volumes.
On the other hand, transfer die stamping uses a different die at each station, performing a different stamping technique. If there are multiple stations, there will be multiple dies. This allows the machine to be flexible – often completing intricate designs at specific angles. It also makes it ideal for larger parts with intricate designs.
3. Progressive Stamping is more Cost-Effective for Higher-Volume Projects
Depending on the design and quantity needed to produce, progressive stamping is often more cost-effective than transfer stamping because of its reduced lead times. Investing in this advanced technology presents a higher upfront cost than transfer die stamping, but offers lower operational costs due to its efficiency.
Transfer die stamping typically has higher operational costs than progressive stamping – not only because it’s more time-consuming, but also due to the fact that it’s able to complete highly complex shapes.
Resource: Engineer’s Guide to Progressive Die Design & Innovation
4. Transfer Die Stamping is More Versatile
Progressive stamping can only accomplish a limited number of stamping procedures with a single die. Transfer die stamping, alternatively, has more capabilities, including:
- Ribs
- Holes
- Cutouts
- Threading
- Knurls
This makes transfer stamping more versatile than progressive stamping, which would require an additional step to accomplish these techniques or finishes.
What do Progressive Die and Transfer Die Stamping Have in Common?
You may already notice plenty of commonalities between progressive dies and transfer dies. Let’s lay them out below:
- Precision: Progressive and transfer dies can both achieve tight-tolerance stamping with complex designs and shapes.
- Minimal waste: Both processes use an optimal amount of metal, leaving minimal waste.
- Suitable materials: Stainless steel, steel, aluminum, brass, copper, titanium, and others can be used on both progressive and transfer dies.
- Applications: Progressive and transfer dies are typically used to create tight-tolerance parts across a range of similar industries, including the automotive, electronics, and medical industries.
- Outsourceability: You can outsource these processes by hiring a reputable company that can safely and efficiently operate the machinery, saving time and potentially reducing costs.
Transfer vs. Progressive Die Stamping: Which is Best?
In general, if your project requires a high volume of small parts with a simple design, progressive stamping could be the right fit. But if your project requires additional cuts or techniques like cutouts or threading, a progressive die won’t be able to complete the project in a continuous run, which will add some time and costs to the project.
If you have a smaller-quantity project with larger, more complex designs, a transfer die might be best suited for your project. However, prepare for it to take longer than progressive stamping would, and potentially cost you more in the long run.
You May Also Like
These Related Stories
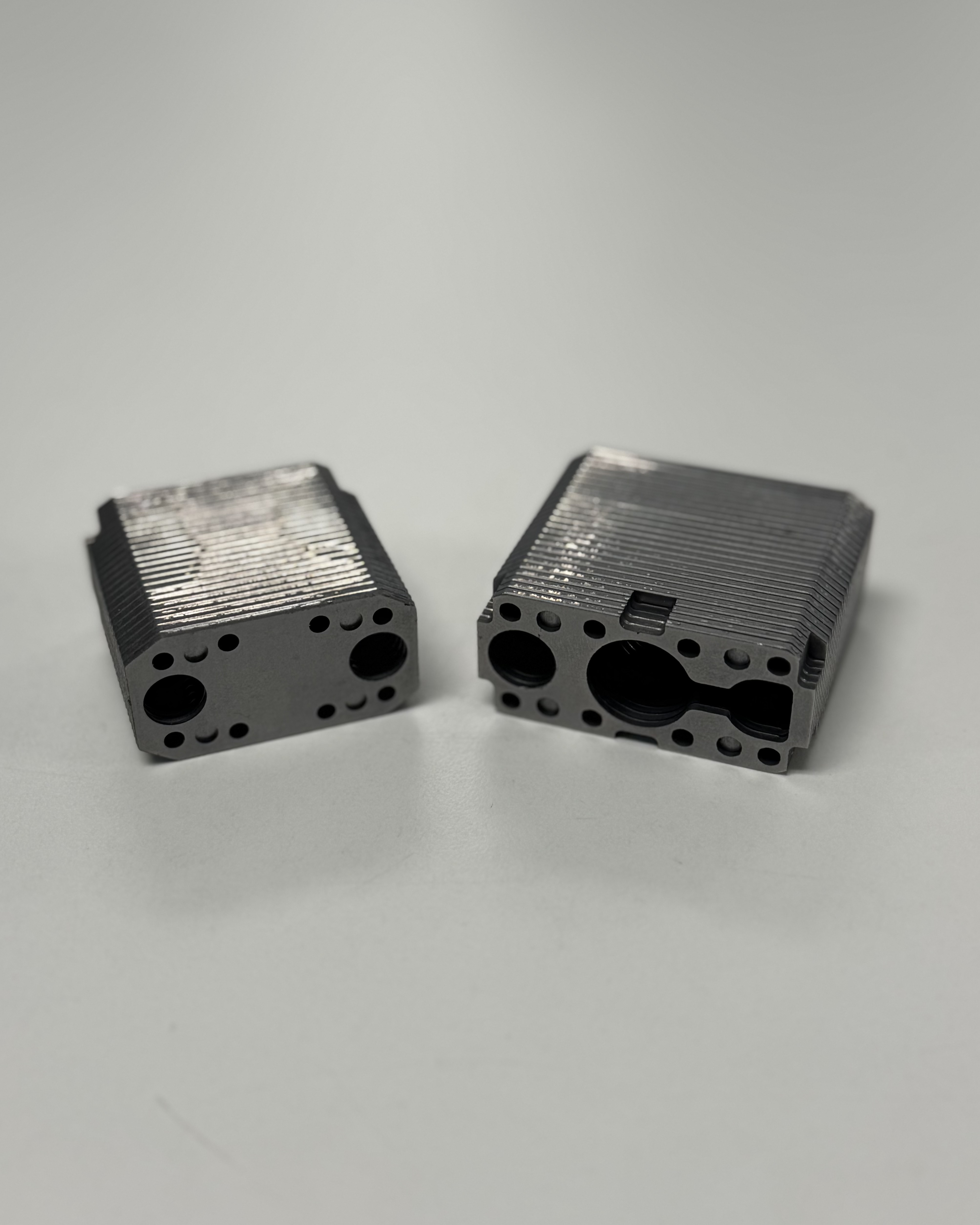
How Lamination Tooling Enhances Precision Stamping
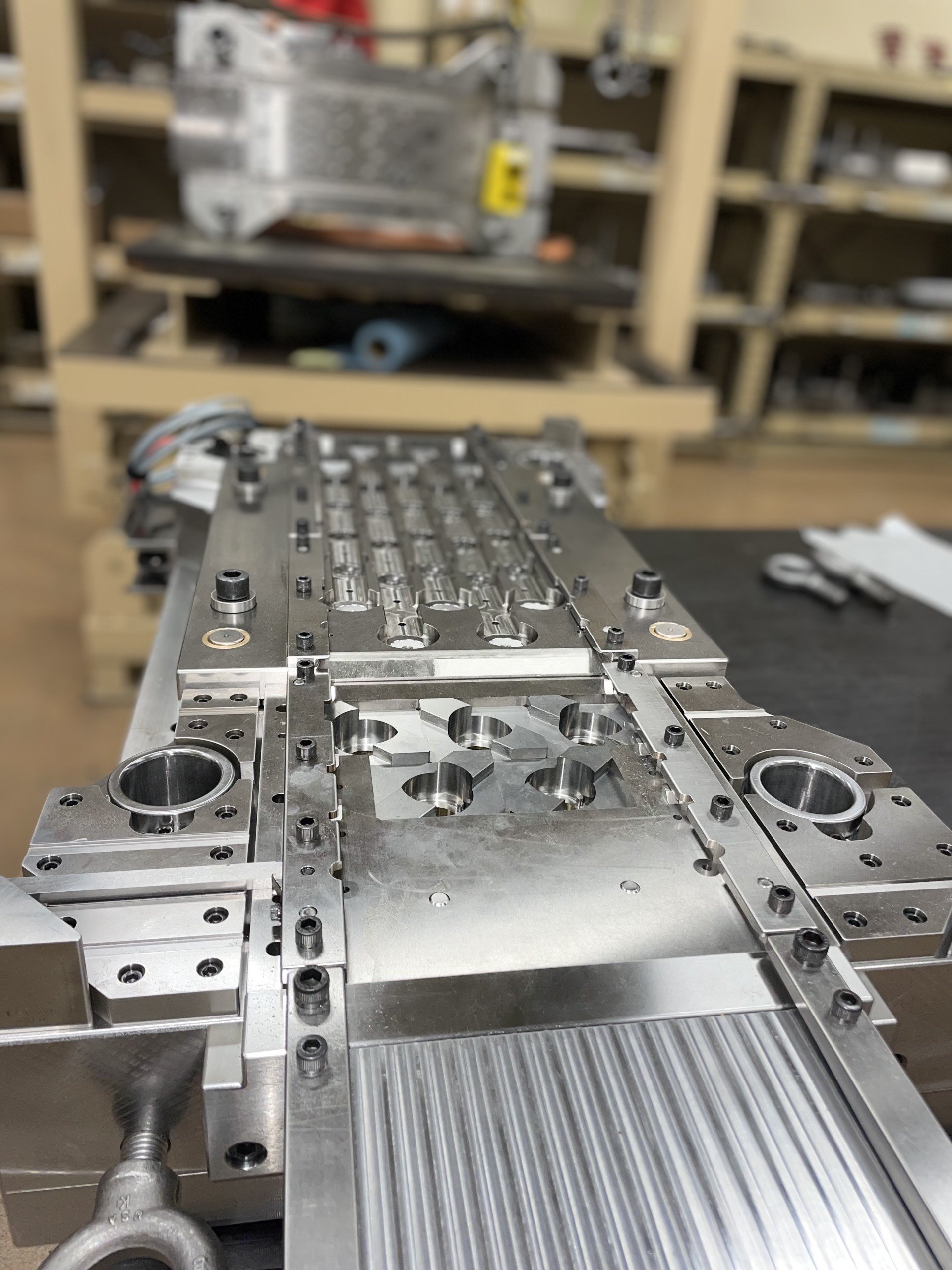
Progressive Die Stamping: An Overview
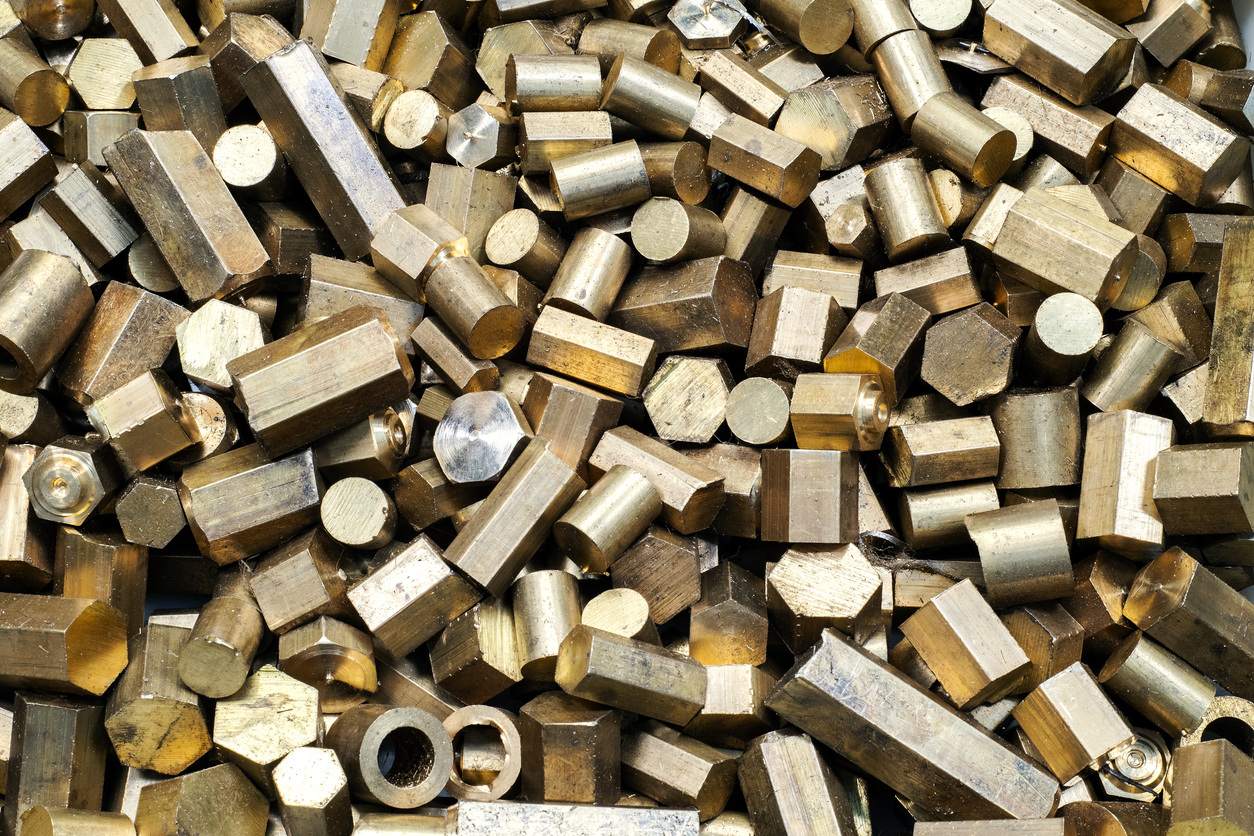