The Solid 6 Types of Stamping Dies
The Solid 6 Types of Stamping Dies
Metal stamping is the backbone of modern manufacturing. It helps create precise, high-quality components for everyday products. Stamping dies are key in shaping metal into functional forms, from automotive parts to consumer electronics.
However, selecting the right die type is crucial because it directly impacts production efficiency, quality, and costs.
If you've been wondering which stamping die is best suited for your needs or how to optimize your operations by leveraging stamping technology, in this article, we will explore the following:
- Different types of stamping die
- Their applications
- Factors that should guide your choice
Types of Stamping Dies
Whether dealing with small batch runs or high-volume production, understanding the six common types of metal stamping dies can help you select the best technique for your next project:
- Single station dies
- Blanking dies
- Piercing dies
- Compound dies
- Multi station dies
- Transfer dies
1. Single Station Dies
Single-station dies are designed to perform a singular operation with each press stroke. They are typically used for straightforward tasks such as cutting materials into specific shapes or punching holes in a workpiece. They offer a focused approach to material processing.
The simplicity of single-station dies makes them easy to design, set up, and operate, which makes them ideal for small production runs or pilot projects. This straightforward design facilitates quick troubleshooting and adjustments, allowing for flexible manufacturing solutions.
Despite their benefits, single-station dies can be inefficient for large production volumes, as each operation is performed one at a time. This limitation can slow production and increase labor costs, especially for complex parts requiring multiple operations.
2. Blanking Dies
Blanking dies are specialized tools designed to cut a piece of material, known as a "blank," from a larger metal sheet. These blanks are the foundational shapes for producing complex part designs.
Blanking dies' primary advantage is their ability to produce clean, precise cuts, which makes them well-suited for high production volumes. Additionally, they minimize material waste, which is both cost-effective and environmentally friendly.
A common challenge with blanking dies is the potential for edge contractions, which can require additional post-processing to achieve a smooth finish. This step adds complexity to the manufacturing workflow and may impact overall efficiency.
3. Piercing Dies
Piercing dies cut holes into metal sheets, creating gaps, slots, or openings. They are often used in conjunction with other dies for multi-stage projects, providing versatility in design and application.
A key feature of piercing dies is their ability to produce crisp, burr-free openings, making them invaluable for high-precision applications. Their precision is beneficial in industries where accuracy is highly important, such as aerospace and automotive manufacturing.
Frequent tool maintenance may be required due to wear from piercing operations, especially when working with thicker or more challenging materials. This maintenance requirement can increase downtime and affect productivity.
Resource: Stay on top of your tool maintenance,
learning how to maintain the life of them here
4. Compound Dies
Compound dies are engineered to perform multiple operations simultaneously in a single stroke, such as cutting and punching. Each action occurs in one press cycle, enhancing efficiency and reducing manufacturing time.
These metal stamping dies are commonly used for tasks requiring high-speed metal stamping accuracy, such as producing parts for electronics or medical equipment. Their ability to perform complex operations makes them valuable in these specific types of precision manufacturing.
While compound dies offer improved efficiency, they can be expensive to design and produce due to their complexity. As a result, they are best suited for high-volume, high-precision production runs where their cost can be justified.
5. Multi Station Dies
Multi station dies, also known as progressive stamping dies, are designed to perform multiple operations across several stations in a single press cycle. As the material feeds through each stage, it undergoes successive operations like cutting, punching, and bending until the final part is complete.
These dies are key for industries producing high volumes of consistent parts, such as the automotive and aerospace sectors. Their ability to streamline production processes makes them a preferred choice for high-demand applications.
Despite their efficiency, progressive stamping dies require advanced press systems and skilled operators to ensure seamless functionality. This increases upfront costs and necessitates specialized training. Outsourcing to an experienced progressive die stamping company can help alleviate these upfront costs by providing access to pre-trained expertise and advanced equipment.
6. Transfer Dies
Transfer dies move individual stamping die components from one station to another, with each station performing an independent action on the part. This setup allows specialized operations at each stage and accommodates complex part designs.
They are ideal for larger, more complex parts that require distinct operations at each station. This flexibility makes them suitable for customized manufacturing needs.
However, transfer systems can be slower than progressive setups, making them less suitable for jobs requiring rapid throughput. This limitation can affect turnaround times and overall production efficiency.
Key Considerations in Die Selection
Selecting the right die can help with efficiency and cost-effectiveness in manufacturing. You can optimize your production process by considering the following:
- Match production volume
- Part complexity
- Material properties
Match Production Volume
When choosing your die, it is best to consider both the production scale and the parts' complexity.
For low-volume production, simpler dies, such as single-station or blanking dies, are cost-effective and easy to set up, minimizing production overheads.
High-volume requirements benefit from sophisticated tools such as progressive stamping dies, which improve turnaround time and reduce per-unit costs. The choice of die largely depends on your batch size.
Part Complexity
Basic dies such as blanking or piercing are ideal for simpler designs and straightforward components like flat panels or single-hole parts. These dies are efficient and cost-effective, providing precision for straightforward projects without complex manufacturing processes. Blanking dies cut flat shapes from sheet metal, while piercing dies create holes, ensuring that parts are produced with clean, accurate edges.
On the other hand, compound or progressive dies are best needed for complex geometries, such as multi-dimensional or intricate components. Compound dies are suited for operations where multiple actions overlap in a single stroke, making them perfect for producing detailed parts that require precise alignment in one cycle. Progressive dies, meanwhile, are designed for high-volume production and perform a series of operations at different stages within the die.
These dies are ideal for intricate shaping, cutting, and forming projects. They allow for efficient mass production without compromising quality. By choosing the appropriate die type, manufacturers can ensure that the project's intricacies are met effectively without incurring unnecessary costs.
Material Properties
Due to their malleability, softer materials like aluminum are compatible with standard dies. This allows smooth and efficient stamping processes. These materials require less force, reducing wear and tear on the dies, making standard options practical and cost-effective.
Contrarily, harsher metals like stainless steel demand stronger and more wear-resistant dies. These materials' hardness and strength necessitate specialized dies that can withstand the increased stress and potential for abrasion during stamping.
Additionally, the thickness of the material is a key factor. Thicker materials can significantly increase the pressure required during the stamping process. Often allowing custom die designs. These custom dies are tailored to manage the added pressure and ensure precise and effective stamping without compromising the integrity of the die or the material.
Choose the Right Stamping Die for Your Needs
Stamping dies are at the heart of modern manufacturing. They offer precision and efficiency in shaping metal into functional parts.
Choosing the right stamping die for your project isn’t just about picking a tool—it’s about aligning your production goals with the die's capabilities. Each type serves a unique purpose, from single-station simplicity to progressive die efficiency.
Basic dies, like blanking or piercing, are excellent for straightforward tasks. However, if your project involves intricate geometries or high-volume production, progressive or compound dies might be the better choice. Also, don’t forget the material—tougher metals require specialized, wear-resistant dies to maintain precision and reduce tool wear.
Ready to Explore the Possibilities?
Do you need expert advice to ensure the best choice for your next production run? Contact us today to discuss your die stamping needs and discover how we can elevate your operations.
You May Also Like
These Related Stories
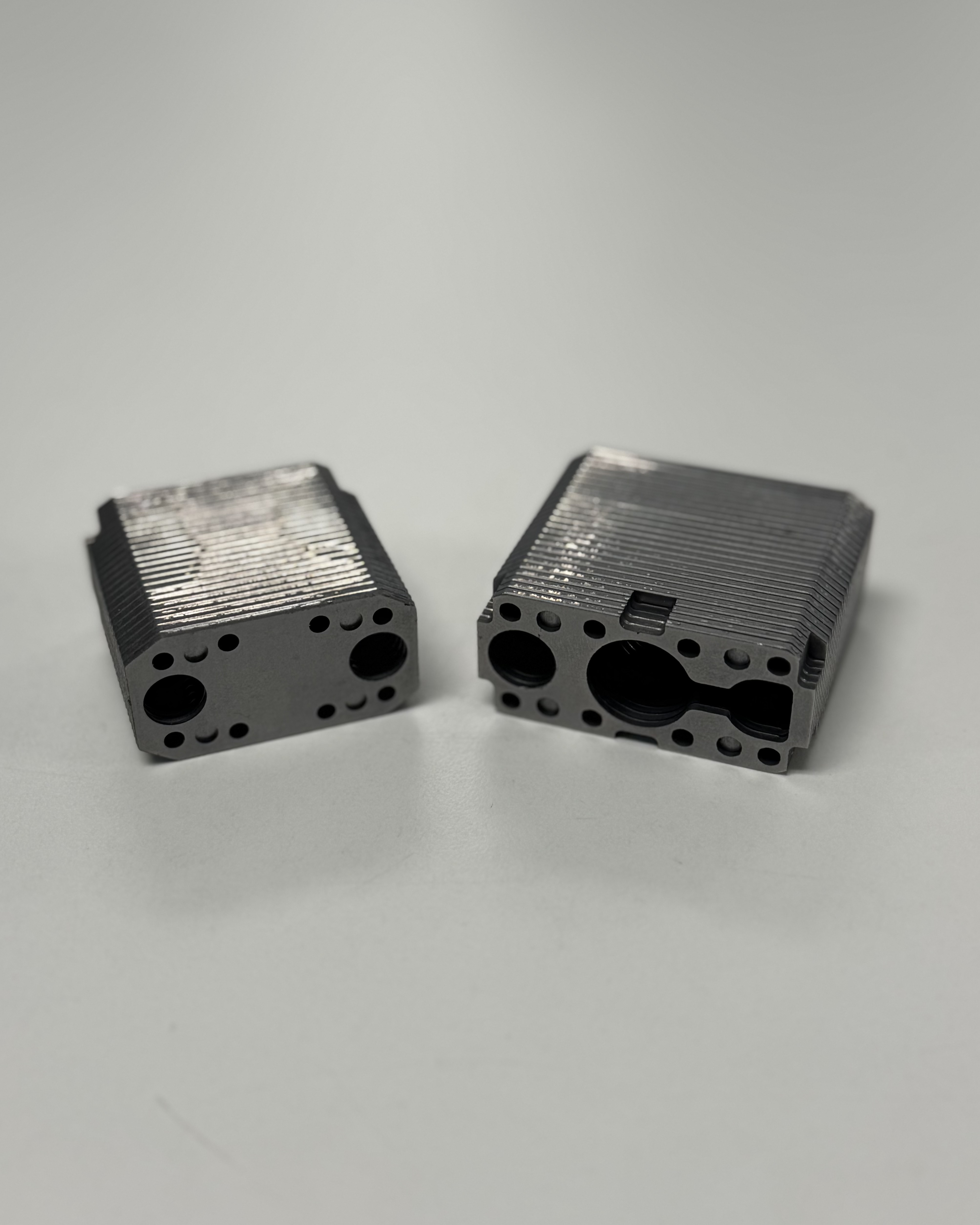
How Lamination Tooling Enhances Precision Stamping
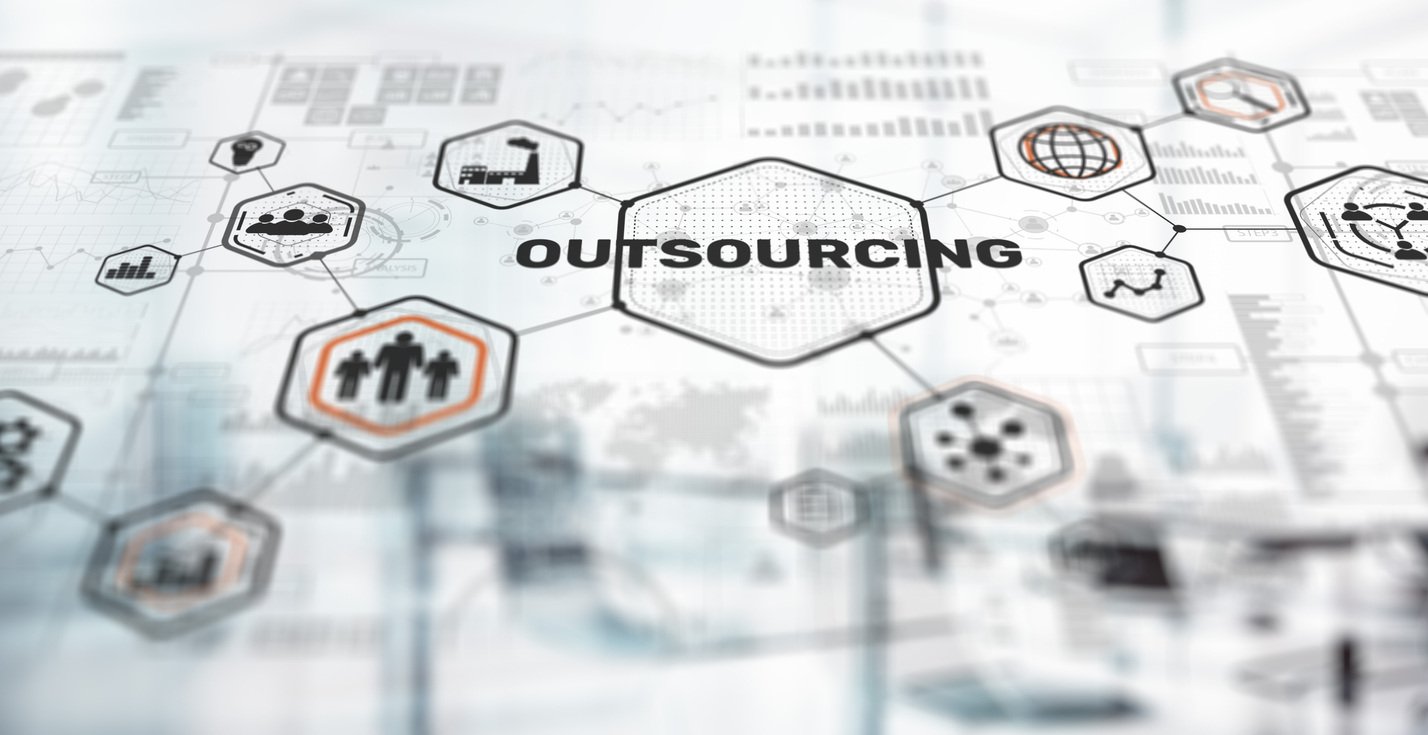
The Power 5 Benefits of Outsourcing for Progressive Die Stamping
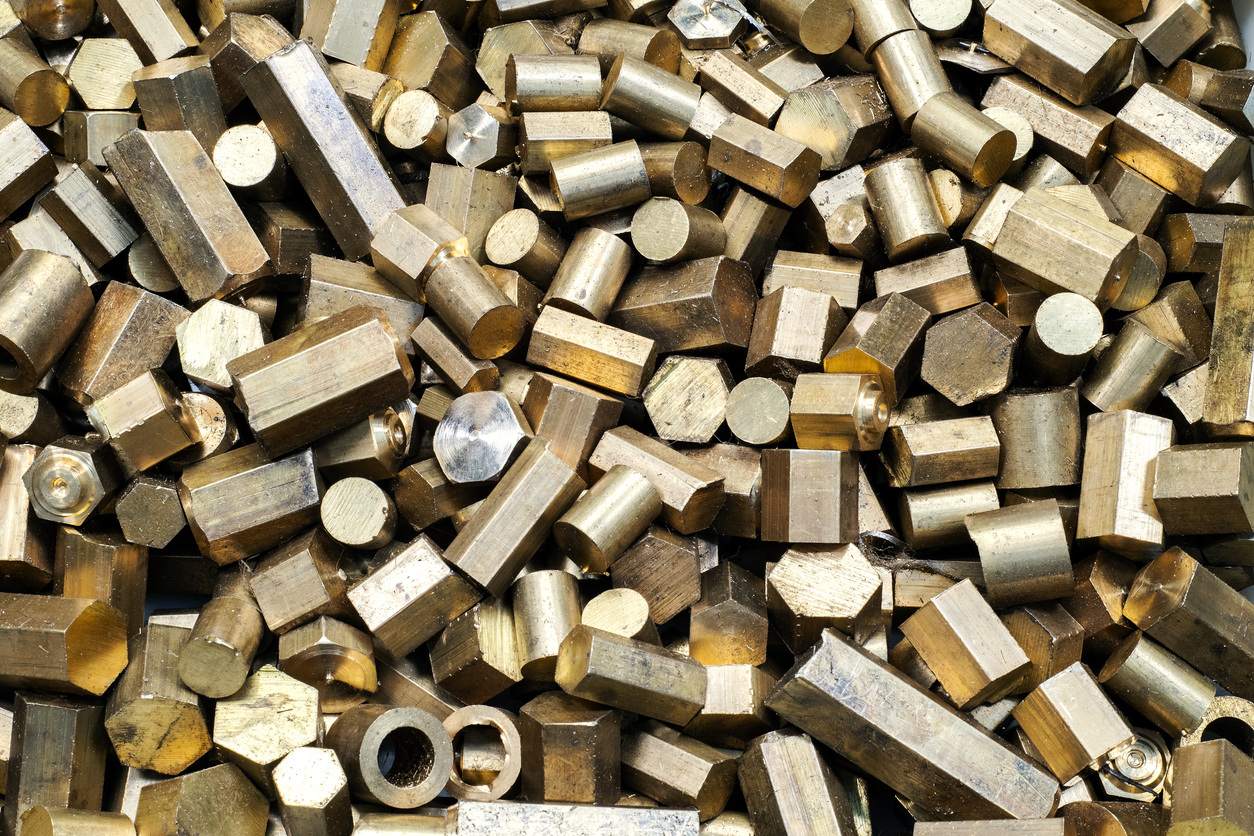