The Metal Stamping Process from Start to Finish
Have you ever wondered how the intricate parts of your favorite electronic devices or even the precise parts of aircraft engines come to life? The answer lies in metal stamping – a versatile and time-tested manufacturing process that transforms flat sheet metal into complex, high-quality parts that shape the world around us.
But what exactly happens during the metal stamping process and what benefits does it have for your production?
Here, we delve into metal stamping from concept to completion. By understanding its various stages, tools, and techniques, we’ll equip you with the knowledge you need to optimize your operations, boost efficiency, and make informed decisions when partnering with a metal stamping provider.
What is Metal Stamping?
Metal stamping is a manufacturing process that involves shaping flat sheet metal into complex and precise three-dimensional parts using dies and specialized machinery, such as metal stamping presses. This process enables the rapid production of high-quality, consistent components in large quantities, making it an essential technique for many industries, including automotive, aerospace, electronics, and more.
Key Stages of the Metal Stamping Process
Metal stamping typically involves the following stages:
- Design & Engineering
- Tooling & Die Making
- Material Selection
- Metal Stamping
- Post-Processing
- Inspection & Quality Control
1. Design & Engineering
In the initial stages of metal stamping, skilled engineers create detailed 2D and 3D models of the desired component using CAD (Computer Aided Design) software. They consider factors such as material selection, tooling feasibility, part geometry, and production efficiency to ensure the design is both functional and manufacturable.
2. Tooling & Die Making
Custom dies are then fabricated using technologies like CNC (computer numerical control) machining and grinding, and wire EDM (electrical discharge machining). These dies are made of high-quality materials, such as hardened steel or tungsten carbide, to withstand high pressures and repeated use during the stamping process.
3. Material Selection.jpg?width=426&height=173&name=iStock-510074526%20(1).jpg)
Next, the appropriate sheet metal material is chosen based on factors like strength, formability, thickness, corrosion resistance, and cost. Common materials used in metal stamping include steel, aluminum, brass, and copper.
4. Metal Stamping
During the metal stamping process, the sheet metal is placed on the stamping die, where it’s held in place by clamps or a magnetic force. As the press activates, the bottom die shoe comes into contact with the press bed. This intense pressure shapes the metal into the desired form, resulting in a precision-made component.
There are several types of metal stamping, including:
-
Progressive Die Stamping
Multiple stations within a single die perform different operations on the sheet metal, progressively forming the part with each stroke of the press.
-
Transfer Die Stamping
A separate transfer system moves the part from one die to the next, allowing for more intricate and complex designs.
-
Deep Drawing
A process in which the sheet metal is drawn into a die cavity to create deep, three-dimensional shapes like cups or containers.
5. Post-Processing
After the stamping process, additional operations may be necessary to achieve the desired final product. These can include:
-
Secondary Forming
Extra forming operations, such as bending, punching, or embossing may be performed to add features or refine the shape of the component.
-
Deburring & Finishing
Removing sharp edges or burrs left from the stamping process and applying surface treatment like plating, painting, or polishing to improve aesthetics, corrosion resistance, or other properties.
-
Cleaning
Thoroughly cleaning the parts to remove any residual oils, lubricants, or debris from the stamping process.
6. Inspection & Quality Control
The finished parts then undergo a rigorous inspection to ensure they meet the specified quality and dimensional requirements. This may involve visual inspections, measurements, and functional testing. Advanced inspection equipment, such as coordinate measuring machines (CMMs) and optical comparators, are often used for precise and accurate assessments.
Benefits of Partnering with an Experienced Metal Stamping Provider
Outsourcing your metal stamping needs to a trusted partner can offer numerous advantages, such as:
- Advanced Equipment & Expertise: By leveraging state-of-the-art metal stamping machinery and knowledgeable professionals, you’ll achieve superior quality and efficiency in your production processes.
- Cost Savings: Partnering with a dedicated metal stamping provider can help you reduce tooling, labor, and maintenance costs while optimizing material usage.
- Timely Delivery: A reliable metal stamping partner will ensure your components are manufactured and delivered on time minimizing disruptions to your production schedule.
- Customization & Flexibility: With a wide range of metal stamping capabilities, an experienced provider can accommodate your specific project requirements and adapt to changes in your production needs.
Unlock the Potential of Your Manufacturing Process with Expert Metal Stamping
By understanding the ins and outs of the metal stamping process, you can make informed decisions to optimize your manufacturing operations and achieve exceptional results. Whether you’re seeking to enhance production efficiency, reduce costs, or ensure consistent quality, partnering with an experienced metal stamping provider can elevate your business to new heights.
You May Also Like
These Related Stories
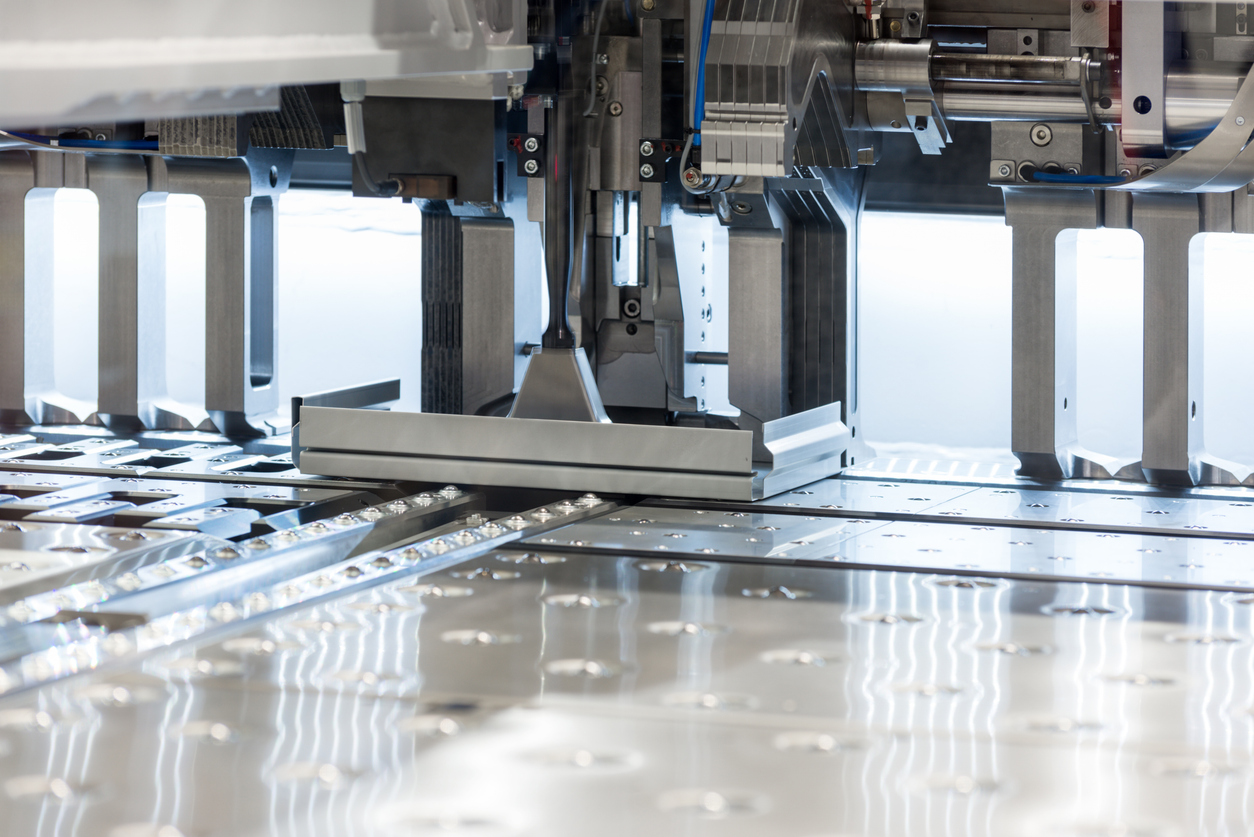
High Speed Stamping: Processes, Use, Pros, & Cons
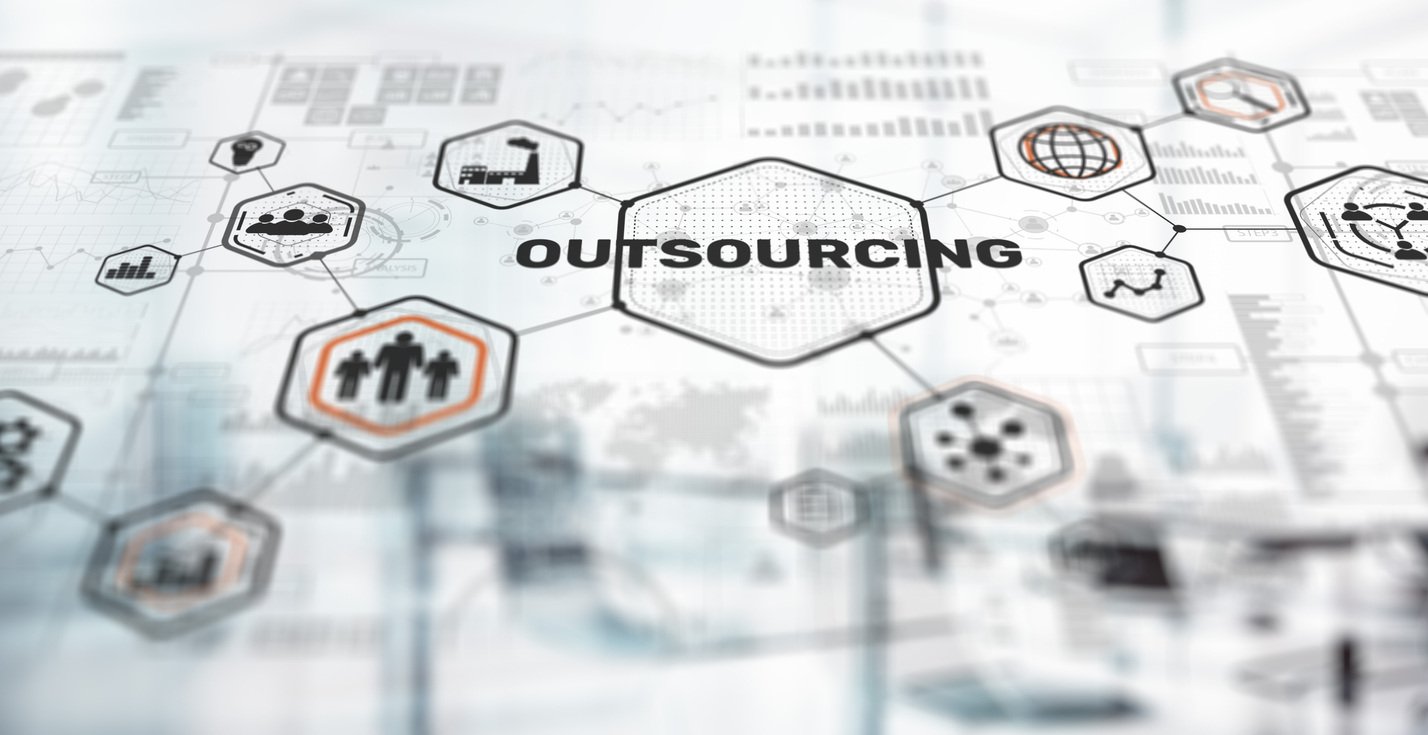
The Power 5 Benefits of Outsourcing for Progressive Die Stamping
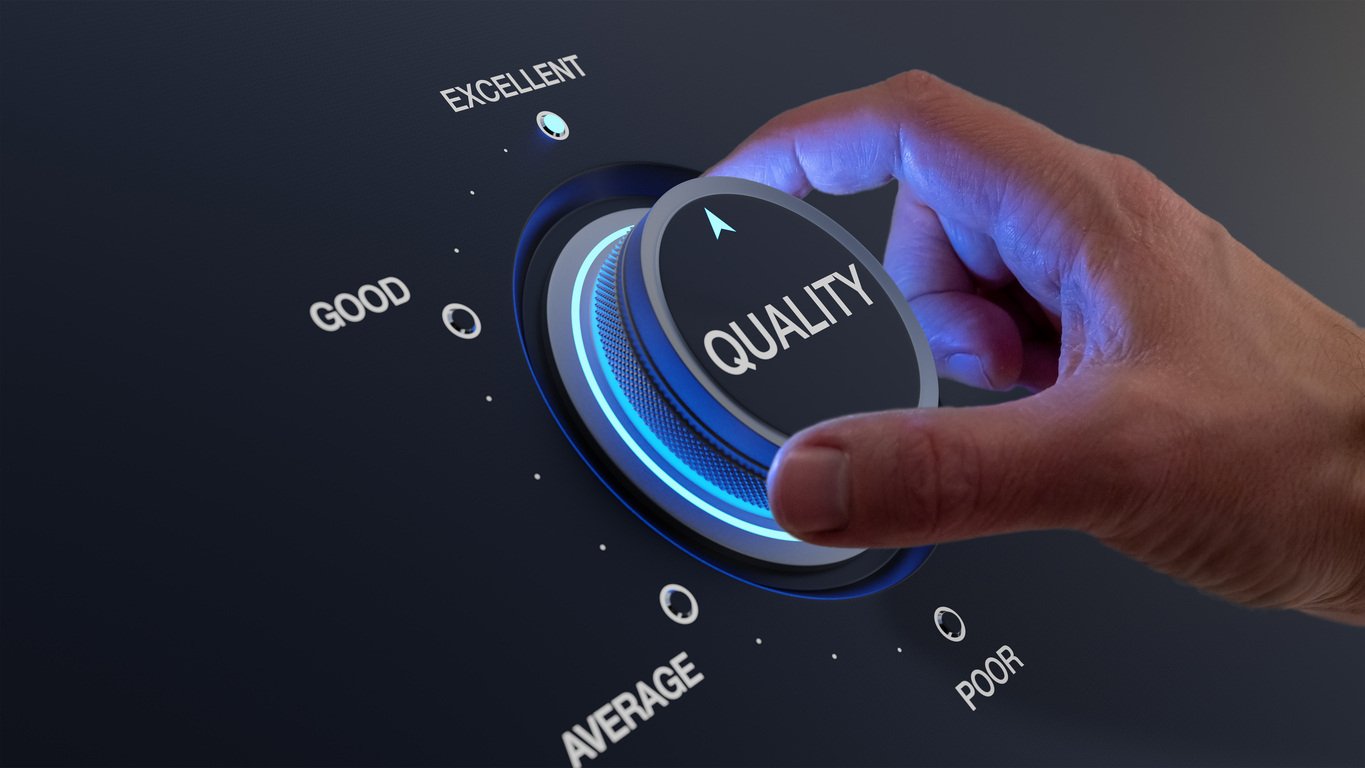