Progressive Die Stamping: An Overview
Though no two projects are the same, there are some universal elements of production that all can benefit from:
Efficiency.
Versatility.
Cost-effectiveness.
Timeliness.
When it comes to transforming sheets of raw metal look no further than progressive die stamping. A sophisticated metalworking method, progressive die metal stamping brings a level of optimization to even the most complex or high-volume orders.
In this guide, we’ll take a deep dive into this fabrication technique, looking at:
- The progressive die stamping process
- The advantages of progressive die stamping
- Comparing other metalworking processes
- & more
What is Progressive Die Stamping?
Valued for its ability to maintain consistency throughout high volumes of production, progressive die stamping involves cutting and forming raw metal sheets through a series of stations on a continuous run. Stamping stations can include:
- Coining
- Bending
- Cutting
- Lancing
- Extruding
- Drawing
- Embossing
- Punching
Resource: Intro to Die Stamping Tools - How Do They Work?
During this metal fabrication method, a metal strip is fed through a series of stamping stations. As each station performs its operation, the strip is moved down the press in sequence. At the end of the run, the metal strip is turned into a finished piece – with all metal forming operations happening quickly in succession in one place.
Ultimately, this reduces the amount of processing steps involved and makes for better production efficiency.
Components of a Progressive Die
What comprises a progressive die?
Multiple stations that perform a series of operations in sequence, which include the following:
- Die stations
- Punches and pilots
- Feed mechanisms and stripper plates
Die Stations and Their Roles
In general, stamping dies perform two primary functions: cutting and forming.
Cutting
Cutting dies typically consist of sharp-edged tools that exert force to shear or separate the metal along specific contours. Common cutting operations in progressive die stamping include:
- Shearing: Produces straight-line cuts in the metal sheet, resulting in pieces with clean, precise edges.
- Blanking: Removes a portion of the metal strip along a defined contour, creating the desired workpiece while leaving behind scrap material.
- Piercing: Creates holes or openings in the metal sheet by removing specific areas of material, often used for functional or decorative purposes.
- Trimming: Removes excess material from the perimeter edge of a formed part, ensuring it conforms to the desired profile without any flash or burrs.
Forming
Forming operations involves shaping the metal workpiece into desired geometries, imparting depth, contours, and features. These operations utilize forming dies, which exert pressure on the metal to deform it without cutting through. Common forming operations include:
- Bending: Curves or shapes the metal along specific axes, creating angles, curves, or bends in the workpiece. Bending dies apply force to the metal to induce plastic deformation along the desired contour.
- Flanging: Bends the edges of the metal sheet along a curved axis, producing raised or folded edges. Flanging can be achieved through stretching or shrinking the metal, depending on the desired result.
- Drawing: Pulls the metal into a die cavity, displacing material to create complex shapes with consistent thickness. Drawing dies exert tension on the metal to stretch it into the desired form, maintaining uniform thickness throughout.
- Stretching: Increases the surface area of the metal sheet by thinning and elongating it. Stretching dies apply tensile force to the metal, causing it to elongate and become thinner while maintaining its overall dimensions.
Punches and Pilots for Precision
In fabrication of any sort, there’s no question what role precision plays – even being off by fractions of a centimeter can be enough to send a finished piece to the scrap pile. Providing stability and guidance, punches and pilots in progressive stamping each help shape & move the strip metal as it’s formed to ensure that it meets specifications.
- Punches: provide force into the die to form it into the desired shape
- Pilot: essentially a pin that holds the metal strip in place as it moves seamlessly from station to station
Feed Mechanisms and Stripper Plates:
Feed mechanisms and stripper plates are what make high-volume production through this metal forming process possible at a consistent rate.
Feed Mechanisms
Feed mechanisms are essentially what move the materials (usually metal) down the die for stamping, efficiently and at a high volume. There are three common forms of mechanisms:
- Roll feed: feeds the material from the roll or coil into the die to be stamped.
- Strip feed: feeds the material through the die by a cut or desired width
- Blank feed: feeds individual pieces of the material into the die
Stripper Plates
After each stamping process, the stripper removes the completed object from the punch. Stripper plates provide a smooth ejection of the part from the die cavity and stop it from adhering to the punch. To increase overall productivity, they facilitate a quick injection of completed pieces.
Advantages of Progressive Die Stamping
While there are many types of metalworking methods available – including other stamping processes – progressive die metal stamping offers several benefits that are hard to ignore.
It should come as no surprise why it’s become a go-to means to create finished pieces of varying complexities.
What does progressive die stamping bring to the table?
- High Efficiency: Able to make short work of a long run, this stamping method is synonymous with rapid production, minimal downtime, & maximized output.
- Cost-Effective: Through its level of automation, you’ll see reduced labor costs and material waste for enhanced cost efficiency.
- Precision: Meeting tight tolerances and consistent quality are no issues.
- Complex Parts: Capable of producing complex geometries in a single operation, saving time and resources.
- Versatility: Accommodates various materials like metal, plastic, and composite material (more on this next)
- Low Scrap Rates: Minimizes material waste through stripper plates, optimizing resource utilization.
- Scalability: Easily scales production to meet demand fluctuations efficiently.
A Look at Progressive Stamping Die Materials & Applications
As we mentioned, progressive die stamping can be used to form a variety of materials. Metal is the primary material used in this fabrication process, though it can also be used on certain plastics and composite materials.
For metalworking, both ferrous and nonferrous metals can be stamped. The most common metals run through progressive stamping include:
- Steel
- Stainless steel
- Aluminum
- Copper
- Brass
Certain specialty metals are also good candidates for progressive metal stamping. For instance, it’s not uncommon to see titanium and nickel-based alloys fabricated, as they both withstand corrosion, heat, and physical stress.
Where Progressive Stamping is Often Used
As a versatile and precise metal fabrication process, you’ll see components produced by this stamping method across a host of industries and applications:
- Automotive: Progressive die stamping is critical in the automotive industry for manufacturing large volumes of precision parts such as brackets, panels, and various engine components. This process allows for the rapid production of complex shapes that are essential in vehicle assembly.
- Electronics: In electronics, this technique is used to create small, intricate parts that require high precision, such as connectors, terminals, and shields. These components often require tight tolerances and high repeatability, which progressive die stamping can achieve efficiently.
- Aerospace: For the aerospace industry, progressive die stamping is used to produce lightweight, durable components crucial for the structural and engine parts of aircraft. This includes items like shims, brackets, and various other metal fittings that need to meet stringent regulatory standards.
- Telecommunications: This process is employed in the telecommunications sector to manufacture components found in infrastructure and hardware, such as antenna parts and electronic enclosures. These parts need to be consistently reliable to ensure long-term functionality and service.
- Construction: In construction, progressive die stamping is utilized to make structural components, fasteners, and fittings. These items must be robust and able to withstand environmental stressors, making the high-strength outputs of progressive die stamping ideal.
- Medical: The medical field uses progressive die stamping to create components that are part of medical devices. These parts, such as brackets, small containers, and surgical tools, require high precision and must adhere to strict hygiene and safety standards.
Progressive Die Stamping vs. Other Metal Stamping Methods (+ Chart)
The choice of stamping method for your project significantly influences the efficiency, quality, and suitability of the final product.
Progressive die stamping is renowned for its ability to produce large volumes of complex parts through a continuous series of operations. But how does it stack up against other metal stamping techniques?
Our chart below compares progressive stamping vs. other stamping methods. But first, let’s take a look at the other metal stamping options for your project.
- Single-stroke die stamping: This method involves a simple operation where the die only strikes once to perform a single action, such as cutting or shaping the material.
- Compound die stamping: Utilizes a single stroke to perform multiple operations like cutting and forming simultaneously. It's efficient for creating flat parts with precise dimensions in medium to high volumes.
- Transfer die stamping: In this method, parts are transferred mechanically between multiple stations within a single machine, allowing for the manufacturing of large or complex shapes that require multiple, sequential operations.
- Multislide or fourslide stamping: This versatile method uses horizontal alignments and multiple slides to manipulate the workpiece from several angles simultaneously, ideal for intricate parts with bends and twists.
- Deep draw stamping: Specialized in forming deeper, more voluminous parts than the original metal sheet depth, commonly used for making enclosures like pots and cases.
- Fine blanking: Offers high precision by using high pressures to produce parts with smooth edges and flat surfaces. This process is typically used for high-precision gears and other components requiring minimal post-processing.
Resource: Learn more about other types of stamping processes. Check out our article, “Metal Stamping Processes.”
Method |
Production Volume |
Part Complexity |
Speed |
Cost-Effectiveness |
Setup Time |
Flexibility |
Material Waste |
Repeatability |
Progressive Die Stamping |
High |
Medium to High |
Very High |
Very High |
Long |
Low |
Low |
Very High |
Single-stroke die stamping |
Low |
Low |
Moderate |
High |
Short |
Low |
Low |
High |
Compound die stamping |
Medium to High |
Medium |
High |
Moderate |
Moderate |
Moderate |
Moderate |
High |
Transfer die stamping |
High |
High |
Low |
Low |
Long |
High |
High |
Moderate |
Multislide/fourslide stamping |
Medium |
High |
Moderate |
Moderate |
Moderate |
High |
Moderate |
Moderate |
Deep draw stamping |
Low to Medium |
High |
Low |
Low |
Long |
Low |
High |
High |
Fine blanking |
Medium |
Medium |
Moderate |
Moderate |
Moderate |
Moderate |
Low |
Very High |
Unlock the Efficiency of Your Manufacturing Process with Progressive Die Stamping
There’s nothing like bringing a high level of efficiency and precision to any project.
When it comes to shaping sheet metal into finished pieces, progressive die stamping checks both boxes while also meeting the size and scope of your project.
Speaking of Your Project…
Contact us today to talk about your metalworking needs!
You May Also Like
These Related Stories
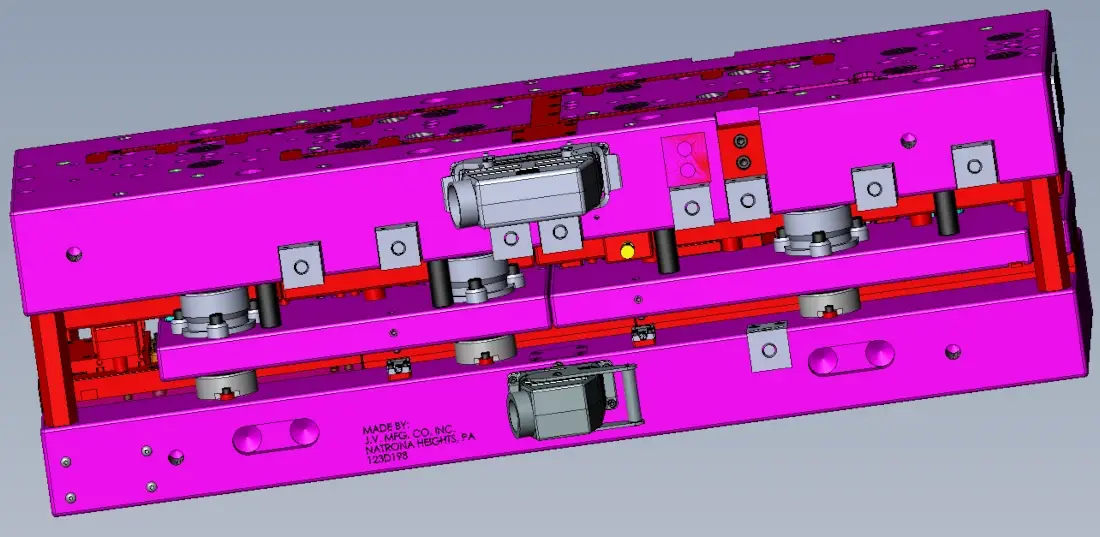
The Engineer's Insights to Progressive Die Design & Innovation
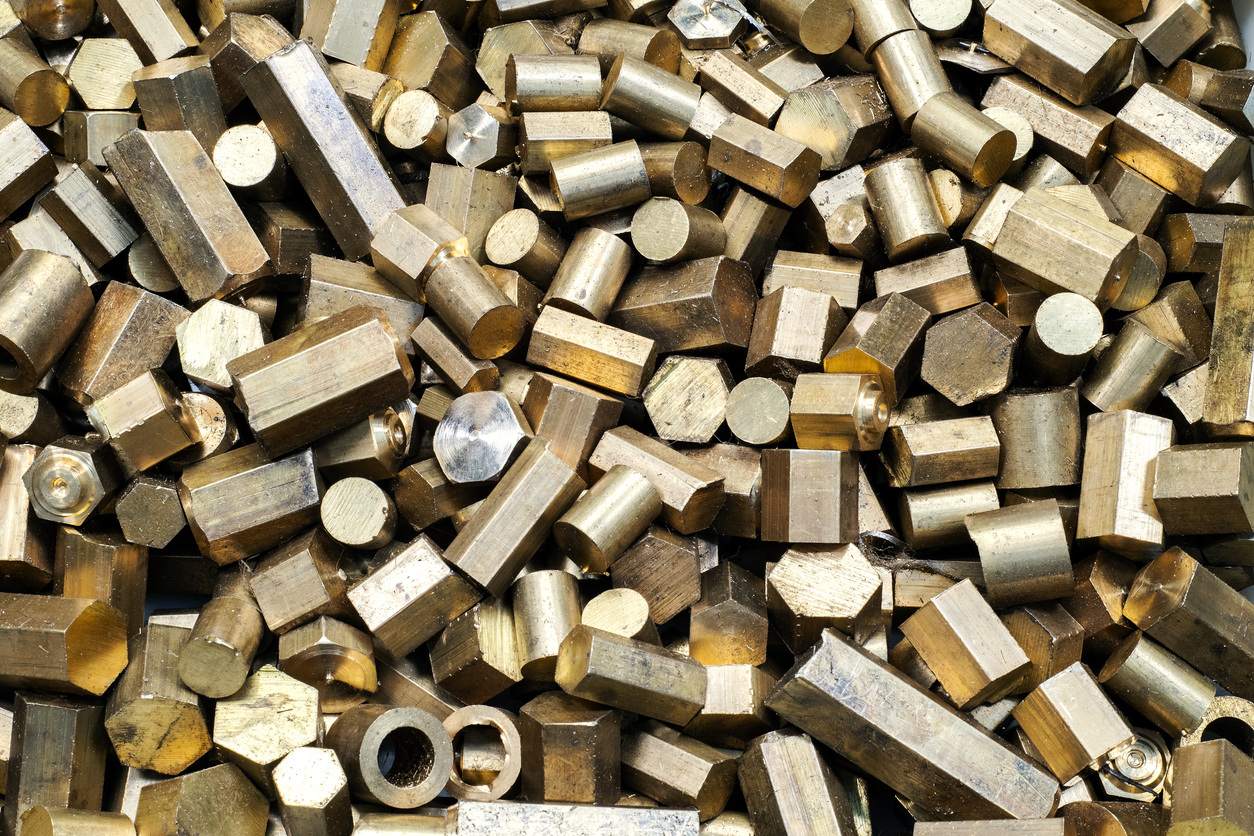
Die Steel Material Choices That Shape Progressive Stamping
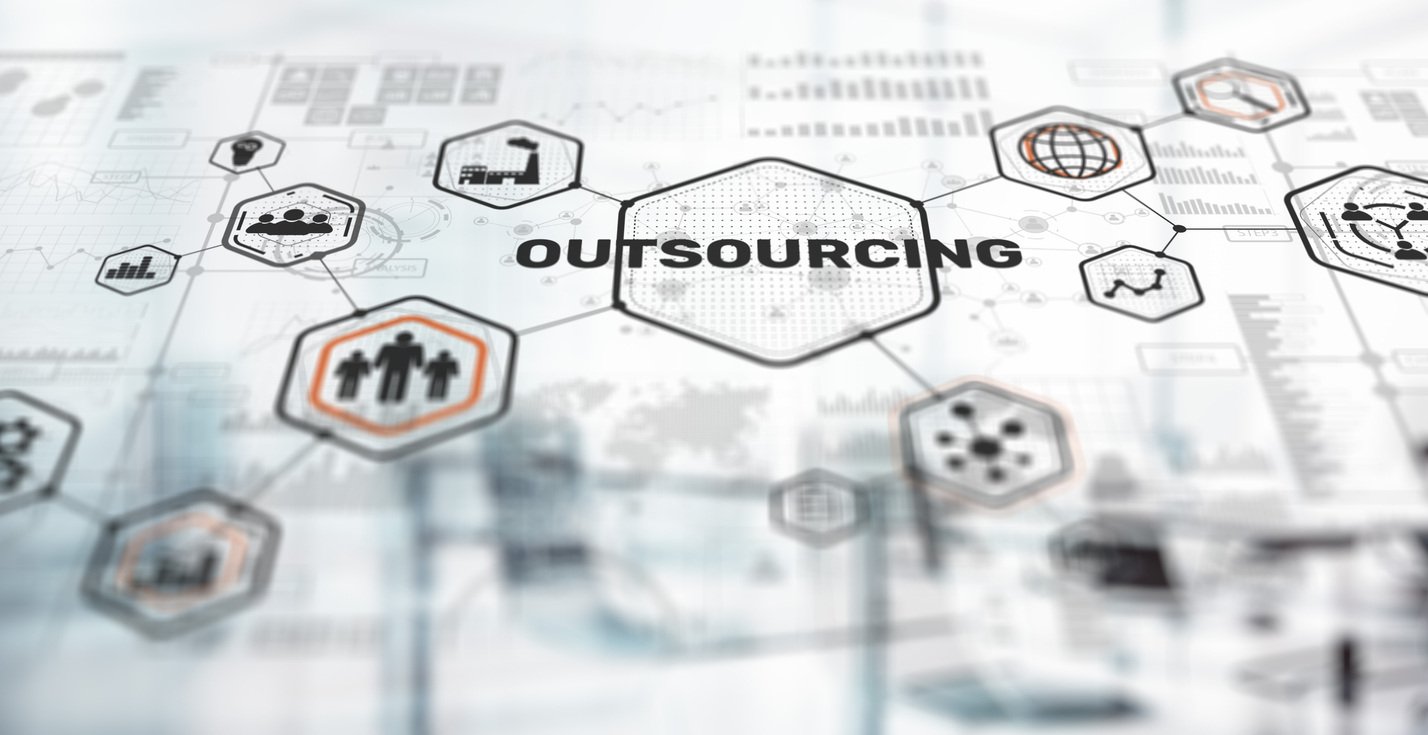