The Engineer's Insights to Progressive Die Design & Innovation
Progressive die design is used in multiple applications that require precision and efficiency in high-volume production. Engineers favor it for its ability to consistently produce accurate parts with minimal waste.
What's the secret to this efficiency? It's in the design process.
Although the basic mechanics of progressive dies are necessary, having a detailed setup and alignment improves their functionality. Because of various considerations, let's examine the when, what, and how of progressive die design (and advanced techniques).
Setting the Stage: Key Steps in Progressive Die Setup
The basic principles of effective progressive die design are not simply about creating tools but creating tools with precision, efficiency, and durability. These tools should be able to produce parts accurately and consistently while handling the harshnesses of repetitive use. The mechanics of progressive dies involve operations performed at different stages within a single press stroke. Each station in the die performs a specific action, such as cutting, bending, or forming, resulting in a finished part at the end of the process. This operational basis allows for high-volume production with minimal manual intervention to improve productivity and reduce production costs.
Setting up a progressive die involves a detailed, step-by-step prep in order to provide optimal performance and longevity. Material handling must be considered, provided that the strip stock is correctly aligned and fed through the die. Accurate die clearance is necessary; if it does not meet clearance requirements, it can lead to excessive wear or failure. The strip layout should be designed to maximize material usage and minimize waste, often using CAD software for accuracy. Followed by securing the die in the press and conducting trial runs to fine-tune adjustments. Attention to detail in these areas provides smooth operation and high-quality output in the progressive die stamping process.
Want to learn more?
Resource: Progressive Die Stamping: An Overview
Best Practices: Proper Installation Techniques for Die Components
Achieving superior die performance requires exact component alignment. This allows each station to operate smoothly, maintaining the integrity and accuracy of the manufactured part. Proper alignment also reduces the wear and tear on the die, extending its lifespan and providing reliable production cycles.
By maintaining tight tolerances and assuring all components are in their correct positions, the die can rapidly function as designed, producing consistent, high-quality parts. This accuracy directly affects the productivity and overall cost-effectiveness of the stamping process.
Alignment issues within the tooling could arise, typically caused by damaged or worn guide components. The main components to monitor are guide pins, guide bushings, and ball cages. Over time, these components may become degraded due to repetitive use and exposure to the high pressures involved in the stamping process. While less common, issues can also occur from damage to dowel holes and dowel pins. This misalignment often results from a die crash or improper installation and removal of components.
What is the best defense against these issues?
Conducting thorough and regular inspections to ensure all guide components are in optimal condition and that dowel pins and holes are undamaged. Corrective actions include replacing worn components, re-aligning parts, or confirming proper installation techniques are followed during maintenance.
Resource: Intro to Die Stamping Tools - How Do They Work?
Cutting Edge Craftsmanship: The Evolution of Progressive Dies & Trends to Watch
Updated technology in progressive die design allows for more exact, consistent production. Some common 3D simulation software programs include:
These programs allow engineers to digitally model and simulate the entire die design process, predicting how materials will conduct under various conditions. This predictive capability helps designers identify potential issues and optimize die geometry before creating physical prototypes, ultimately saving time and reducing costs.
Another innovative technology is laser cutting in die manufacturing. Laser cutting offers precision and speed, creating complex die shapes with tight tolerances. This technology minimizes the need for manual adjustments and additional machining processes, leading to quicker turnaround times and higher-quality dies. By using a 3D simulation and laser cutting, manufacturers can achieve more accurate and efficient die designs, significantly improving the overall productivity of the stamping process.
The future of progressive die design has developed with remarkable advancements driven by emerging technologies and innovative design strategies. Another expected trend is the increased use of artificial intelligence (AI) and machine learning in manufacturing. By analyzing vast amounts of data from past projects, AI can provide insights and recommendations for optimizing die configurations, predicting wear patterns, and enhancing material utilization. This data-driven approach promises to elevate the precision and quality of die designs while reducing the likelihood of errors.
Another trend to watch is the adoption of innovative materials and advanced coatings. These materials can adapt to changing conditions during stamping, maintaining their integrity and reducing wear. Smart coatings can also provide real-time feedback on the condition of the die, allowing for predictive maintenance and reducing unexpected downtime.
Navigating the Challenges of Progressive Die Design
There are three typical problems that progressive die designers face that can be solved by the innovations the industry is adapting to. These challenges and their solutions are:
- Material Springback: This is where the metal attempts to revert to its original shape after deformation. Using 3D simulation software, engineers can predict springback behavior and adjust the die geometry accordingly to counteract this effect. By including more forming processes or higher forming pressures in the simulations, accurate calibration can be achieved before actual manufacturing. This significantly minimizes inconsistencies in the finished product.
- Die Wear: Die components are exposed to repetitive high-pressure operations, leading to unavoidable wear and tear. Engineers can identify wear-prone areas and apply wear-resistant materials through preventive maintenance facilitated by 3D simulations and inspection tools. They can also add protective coatings to extend the die's lifespan. Regular maintenance schedules based on predictive analytics also play a key role in maintaining the accuracy and quality of the die components.
- Part Distortion: Parts may experience unwanted distortions during stamping processes caused by uneven stresses or imbalances in the die setup. Using advanced laser cutting technology, engineers can achieve high precision in component fabrication, providing uniform material thickness and optimal die clearances. By manufacturing the die design in a digital environment, the consistent distribution of forces can be maintained to minimize part distortions and improve the overall consistency of the stamped products.
These solutions are key to achieving successful and dependable die design, improving productivity, and providing high-quality manufactured components. Two case studies demonstrate a solution to the everyday challenges :
Case Study 1: Managing Material Thinning and Stretching
Engineers faced significant challenges with material thinning and stretching in a complicated project involving the drawing and forming of lightweight aluminum components for the automotive industry.
Excessive thinning led to material cracking and tearing, compromising the integrity of the parts. Failure Mode and Effects Analysis (FMEA) software was used to digitally simulate the drawing and forming processes. By adjusting the die geometry and forming pressure within the simulation, engineers could indicate spring back behavior and identify potential issues with material thinning before creating physical tooling. This proactive approach allowed for refined adjustments in the die design, decreasing the risk of material failure and assuring robust final products.
Key takeaways: Leveraging digital simulations was important for predicting and addressing potential issues in the design phase. By integrating FMEA software into the design process, engineers can deliberately resolve challenges related to material thinning to produce reliable, quality-manufactured components.
Case Study 2: Reducing Tonnage in Progressive Die Setup
A consumer electronics manufacturer experienced difficulties with the tonnage exerted by the stamping press, which overreached the operational capabilities of their existing machinery. The challenge was to adjust the tooling within the die to distribute the force more effectively, allowing the tool to be used in existing customer machines.
The answer involved staggering the punches within the die setup. By spreading the punch operations over a more extended portion of the ram's travel distance, engineers reduced the peak tonnage experienced by the press. This technique allowed the machine to exert a lower tonnage over a more extended period, providing compatibility with current machinery without compromising the quality or functionality of the stamped parts.
Key takeaways: This case highlights the value of innovative die design strategies, such as punch staggering, to manage and reduce peak tonnage. The approach made it possible to use existing machines and highlighted the importance of continuous adaptation in die setup to meet operational limitations and avoid disruptions.
Securing Tomorrow: Precision with Progressive Die Design
Through innovative techniques such as progressive die design, 3D simulations, and laser cutting, designers are meeting and exceeding the demands for high-volume production environments. Continually advancing technology promises a future where precision and adaptability manage manufacturing processes.
Get Precise Results for Your Projects
Don't hesitate to contact us if you want to integrate these cutting-edge design techniques into your manufacturing process. Request a quote today and ensure your production is as efficient, precise, and cost-effective as possible. Let us help you turn challenges into opportunities with progressive die design.
You May Also Like
These Related Stories
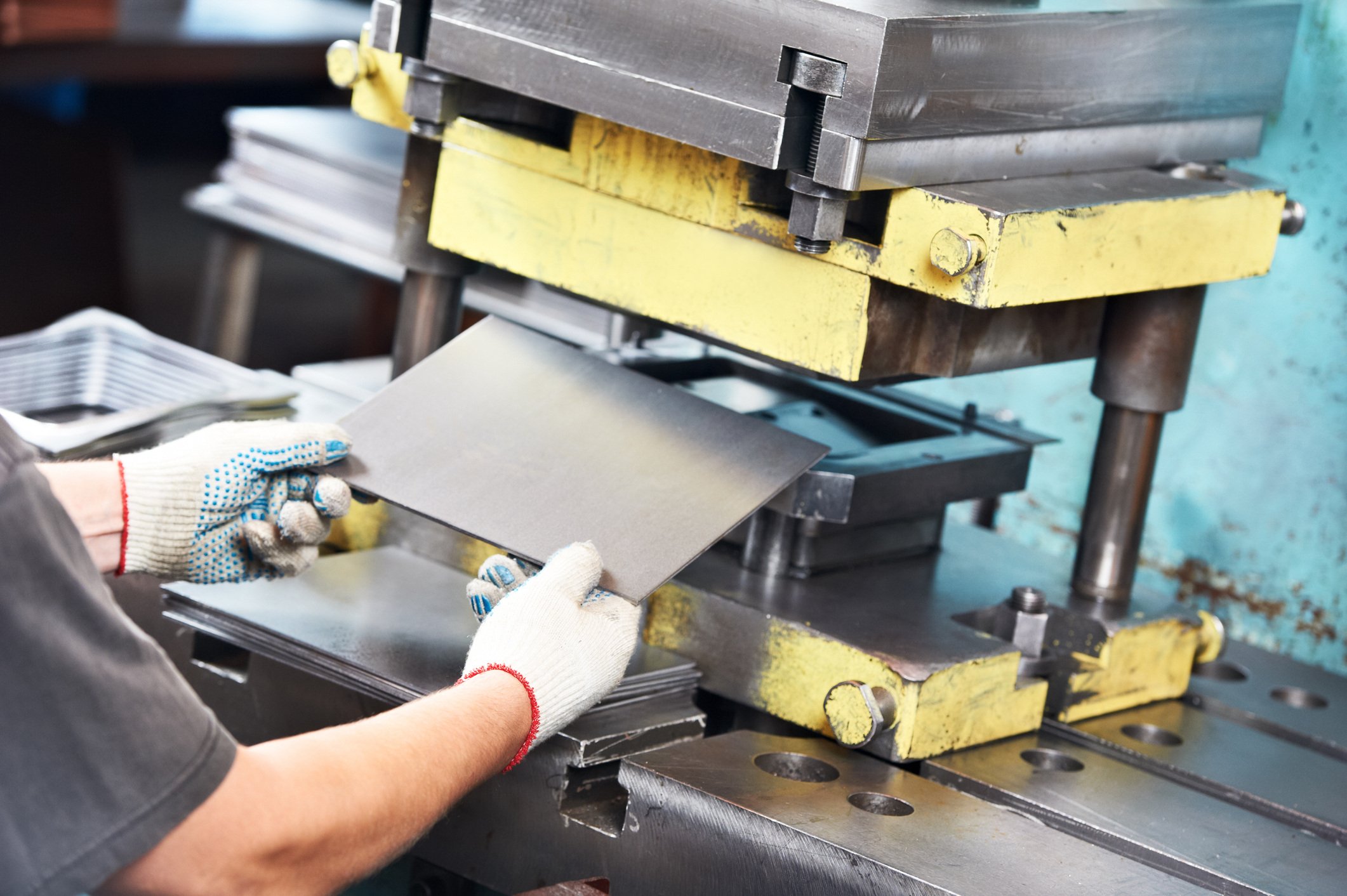
The Solid 6 Types of Stamping Dies
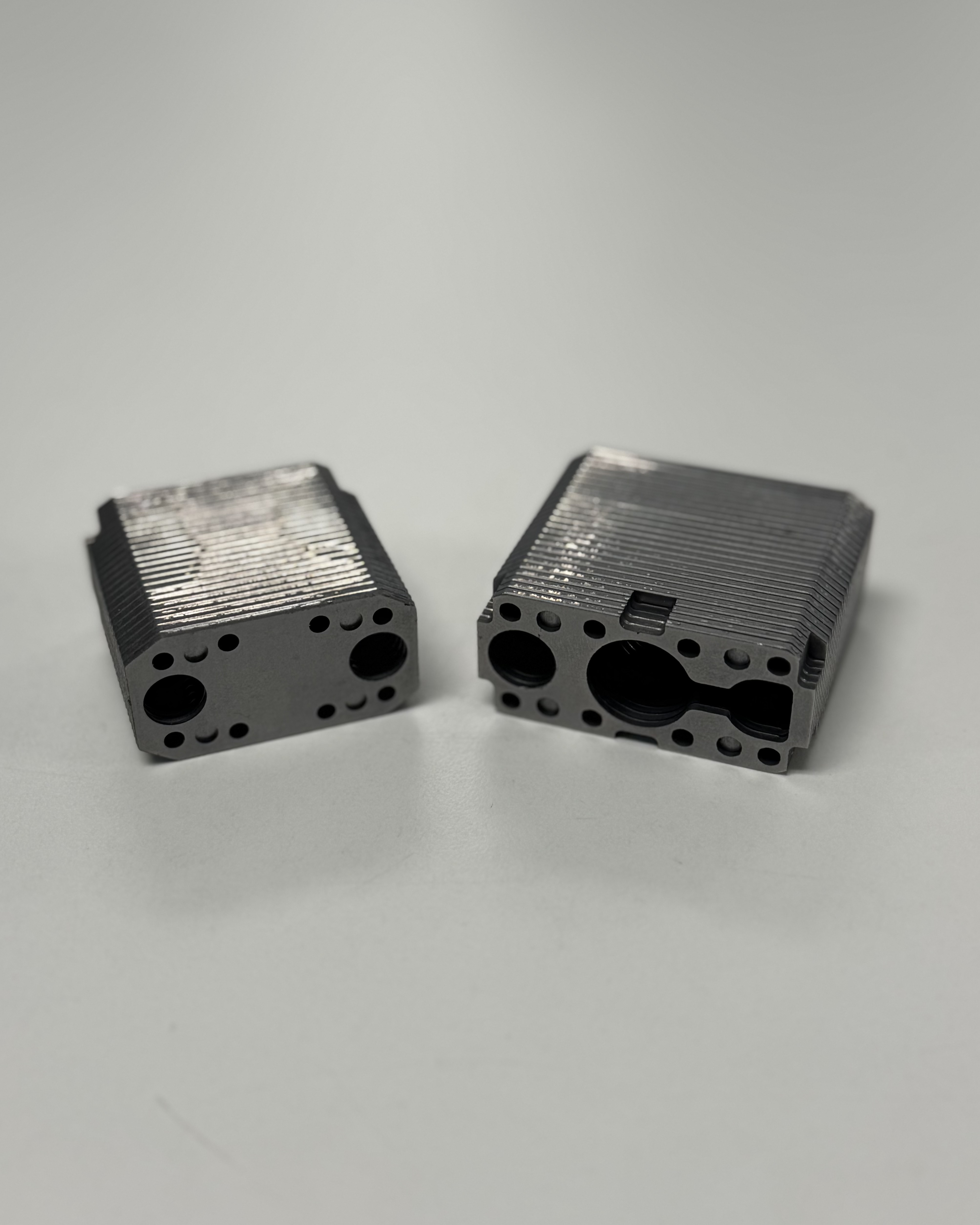
How Lamination Tooling Enhances Precision Stamping
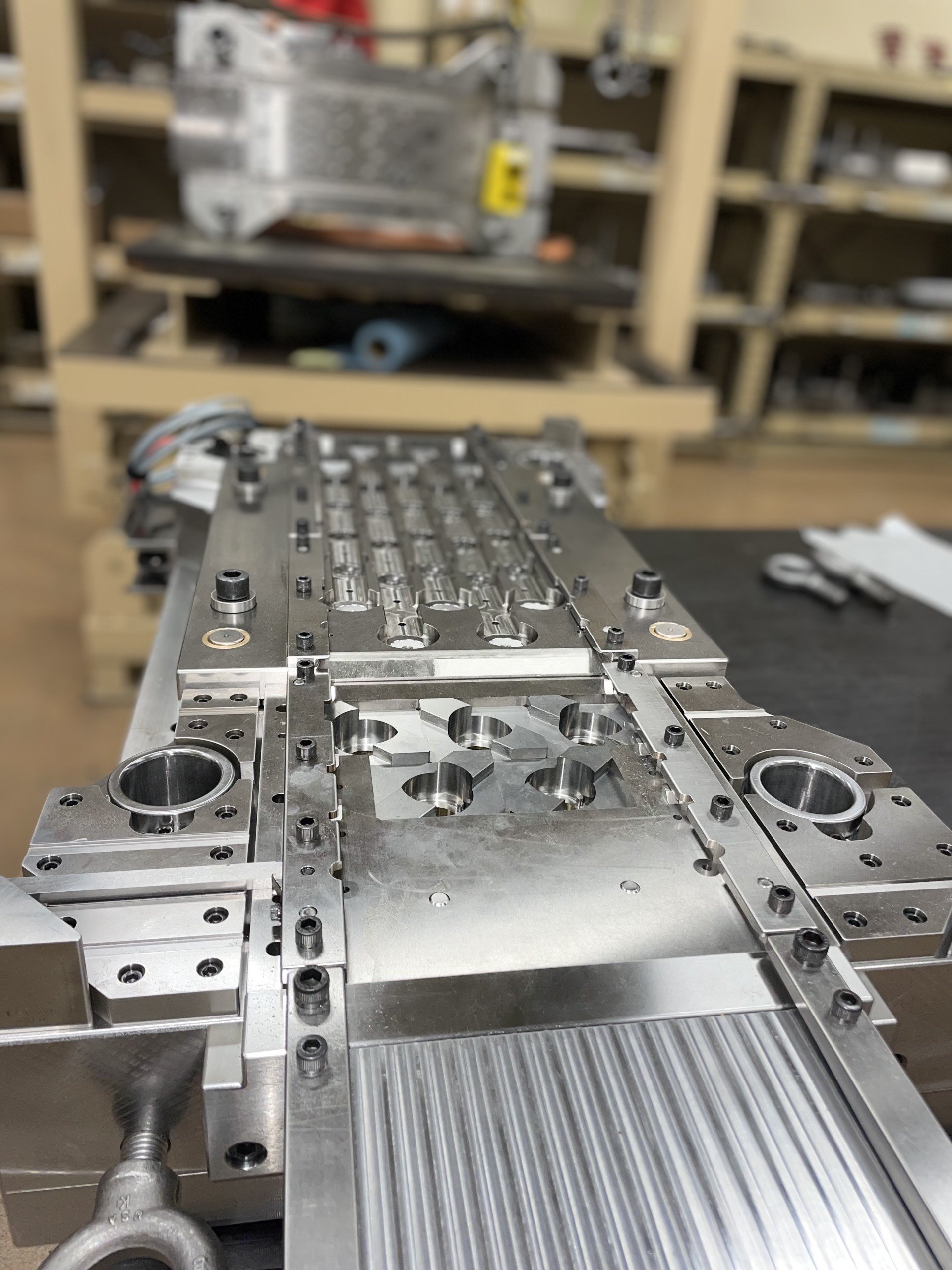