Reducing Manufacturing Lead Time with Progressive Die Stamping
Do you prefer a traditional, slightly less efficient manufacturing setup or the powerful efficiency of advanced die-stamping technology?
Would you instead work with a company that just takes orders or one that actively helps solve problems?
If you're reading this article, you likely recognize that progressive die stamping is a strategic move to reduce manufacturing lead time in metal stamping. This method streamlines the production process, allowing Original Equipment Manufacturers (OEMs) to focus on core competencies, marketing, and research and development.
So, what's your best option?
This might not be your first time considering investing in traditional manufacturing methods or switching to a more resource-abundant, advanced stamping setup. Or it's your first time considering the significant differences between conventional production and progressive die stamping. These differences aren’t always posted clearly as you walk through the factory door.
But know this: the differences are substantial. This article will uncover multiple clear indicators to help you determine which production method will effectively meet your needs and drastically reduce lead times.
Brief Overview of Progressive Die Stamping
Progressive die stamping is a manufacturing process that forms metal sheets into specific shapes and components through a series of sequential operations. This method relies on a series of stations in a single die setup, where each station performs a different operation, such as cutting, punching, or bending. The metal strip is fed continuously through the die, with each step progressively shaping the material until the final product is achieved.
Identifying bottlenecks in the progressive die-stamping process is essential to maximize production efficiency. Key components of the stamping process include die stations, each with a specific role to perform. Each station is designed to carry out individual actions such as:
- Shearing
- Forming
- Bending
Each station plays a significant role in shaping the final output in a progressive die setup. Understanding the capacity and speed of each station can help pinpoint where delays or inefficiencies may occur. For instance, if one station consistently takes longer than others to complete its operation, it becomes a bottleneck that slows down the entire production line.
Punches and Pilots for Precision
Punches and pilots are necessary steps after going through the die stations in the progressive die stamping process to maintain precision throughout the stamping process. Punches create the desired shapes, while pilots align the metal strip within the die. Regular maintenance and inspection of these tools can help address issues ahead of time that might lead to inaccuracies or slowdowns.
Need tips about maintaining tool maintenance?
Learn more about the process here
Feed Mechanisms and Stripper Plates
Efficient feed mechanisms and properly functioning stripper plates are necessary for maintaining a smooth material flow through stamping. The feed mechanism consistently feeds the metal strip to each station, while stripper plates ensure that the formed parts are removed cleanly from the die after each operation. Any malfunction in these areas can lead to production delays, emphasizing the need for routine checks and improvements. By focusing on these key components, manufacturers can streamline their progressive die-stamping operations and enhance overall productivity.
Why Progressive Die Stamping?
Progressive die stamping is recognized for its efficiency and effectiveness in production:
- Rapid Production: This method dramatically lowers production costs and shortens the cycle due to its continuous high-volume metal stamping.
- Cost-Effectiveness: Its high level of automation minimizes labor involvement and speeds up the manufacturing process, reducing overall manufacturing lead time.
- Single-Operation Complexity: It can create complex parts in one go, eliminating the need for multiple setups and operations and streamlining production.
- Scalability: Easily adjusts to production demands, allowing for swift scaling up or down based on project needs.
- Precision and Consistency: Maintains tight tolerances with consistent quality across large volumes, reducing rework and delays.
- Material Efficiency: Optimizes material use, minimizing waste and enhancing production speed.
Working with various materials improves progressive die stamping's adaptability, making it a preferred method across different sectors.
Impact on Reducing Lead Times
To take on the full potential of progressive die stamping in a competitive manufacturing landscape, there are three key areas of improvement. These not only streamline operations but also adapt to market demands swiftly, making sure manufacturers stay ahead. Here’s how optimizing these aspects can transform market responsiveness:
- Streamlining production processes
- Reduced setup and transition times
- Increase market speed
Streamlining Production Processes
Streamlining production processes in progressive die stamping significantly reduces manufacturing lead times in metal stamping, which is needed in today’s fast-paced manufacturing environment. By optimizing the workflow and operating efficient die designs, manufacturers can improve the speed and efficiency of each stamping operation.
Reduced Setup and Transition Times
Another key factor is minimizing setup and transition times between operations. With well-planned layouts and automated systems, the delay between changing from one operation to the next can considerably decrease. This reduction speeds up the production line and makes manufacturers more responsive to fluctuating market demands.
Increase Market Speed
These improvements result in increased product market speed. As lead times decrease, businesses can deliver products to customers more quickly, securing a competitive edge. This agility in production supports better customer satisfaction and fosters innovation, as manufacturers can swiftly bring new designs and products to market.
Overall, the efficiency gained through advanced progressive die stamping techniques drives substantial gains in productivity and market responsiveness. Manufacturers can receive the numerous benefits of progressive die stamping by continuously monitoring and improving the components and processes.
Read on to learn more about the process in our blog about
Progressive Die Stamping: An Overview
Case Studies and Industry Applications
In the dynamic manufacturing world, case studies provide invaluable insights into practical applications and the transformative impact of technological advancements. These two case studies from food packaging and electrical connectors showcase the effectiveness of progressive stamping tools in significantly enhancing production capabilities.
Food Packaging Application
Faced with the challenge of boosting production, a customer transitioned from producing 200-250 flat plastic components per minute to an astounding 8,000 pieces per minute. This dramatic increase was achieved by conducting an engineering study to optimize material selection and the progression of the parts. The introduction of a JVM-built progressive stamping tool, operated by a strip width, allowing eight parts per stroke, facilitated a production rate of 1,000 strokes per minute on the newly purchased stamping line. The parts remained in the strip post-stamping, simplifying transportation to subsequent operations.
Electrical Connector Application
Another customer aimed to improve output while reducing the lengthy changeover times associated with their diverse catalog of 150 part numbers. By implementing a JVM Modular style tool, the solution allowed for rapid changeovers—reduced to 30 minutes—by merely switching out specific modules. This innovation slashed the stock strip widths to about 10% of the prior requirement and increased the production speed to 300 strokes per minute, potentially exceeding 500 with additional enhancements.
Progressive die stamping offers solutions that increase efficiency and adapt flexibly to diverse production demands. Such advancements highlight the development of manufacturing processes, paving the way for future outcomes that promise even greater efficiency and productivity.
Check out Die Stamping with Other Methods
to learn about what process best suits your needs!
Choosing the Right Progressive Die Stamping Partner
Focusing on how choosing the right progressive die stamping partner reduces manufacturing lead times in metal stamping involves considering several necessary factors:
- Experience
- Technology
- Quality control
- In-house tooling capabilities
Expertise
The partner's expertise in the progressive die stamping field is major. A seasoned provider should have a proven track record with similar projects, demonstrating proficiency in working with various materials and handling complex geometries. Their experience can significantly influence project outcomes, from initial design to final production.
Technology
Advanced technology plays a key role in today's fast-evolving manufacturing landscape. Talk to your stamping partner to ensure they use the latest design, simulation, production tools, and software. Innovative technology streamlines processes, improves precision, and can result in faster turnaround times, boosting overall efficiency and productivity.
Quality Control
A strong quality control system is essential for maintaining high production standards. Assess the partner's quality assurance procedures, including inspection processes and certifications. Effective quality control guarantees that the stamped components meet the required specifications, reducing the probability of defects and the need for costly rework.
Importance of In-House Tooling Capabilities
In-house tooling capabilities are a significant advantage when selecting a progressive die stamping partner. The ability to design, build, and maintain tooling internally allows for greater control over production timelines and quality. It also allows quicker adjustments and improvements to the dies when necessary, resulting in less downtime and a more responsive production environment. Partnering with a provider with in-house tooling capabilities can lead to streamlined communication, faster project execution, and increased efficiency.
Learn about Our Team: Your Die Stamping Partner
Accelerating Success: The Power of Progressive Die Stamping Partnerships
Partnering with a progressive die stamping expert offers strategic advantages, like significantly reducing lead times, which can be crucial in a competitive manufacturing landscape. Choosing a partner like this means prioritizing your production processes' speed, precision, and efficiency.
This collaboration streamlines manufacturing and allows businesses to respond more quickly to market changes and customer demands.
Are You Ready to Improve Your Production Capabilities?
Contact us today to see how progressive die stamping can transform your operations, ensuring you meet industry standards while maintaining cost-effectiveness. Let us guide you through the complexities of modern manufacturing with tailored strategies designed to maximize your productivity and innovation.
You May Also Like
These Related Stories
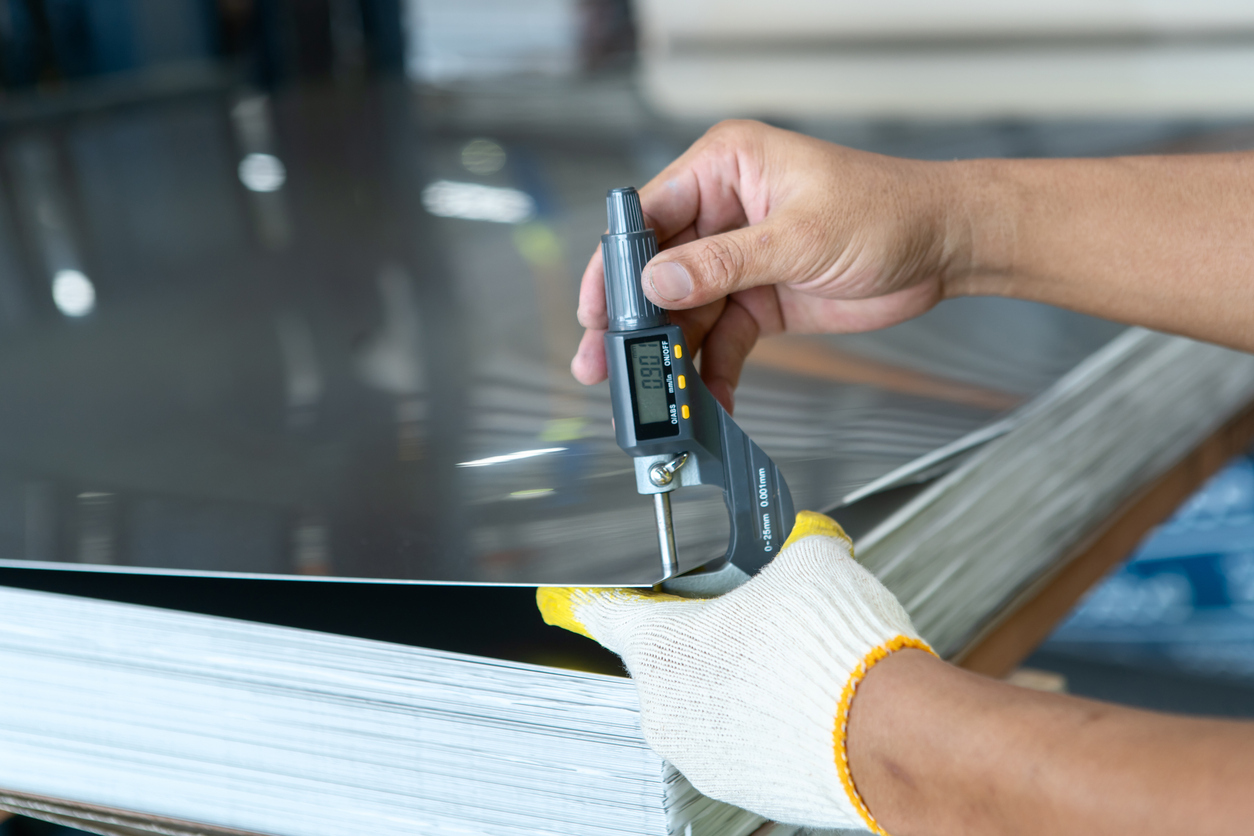
Understanding Stamping Thickness for Metal Stamping Success
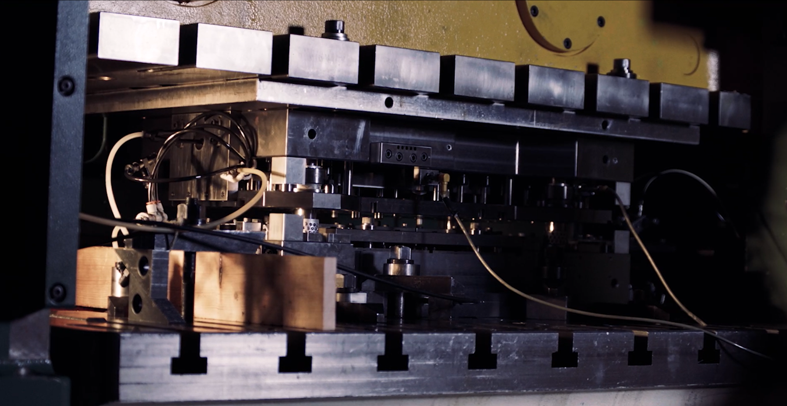
Intro to Die Stamping Tools - How Do They Work?
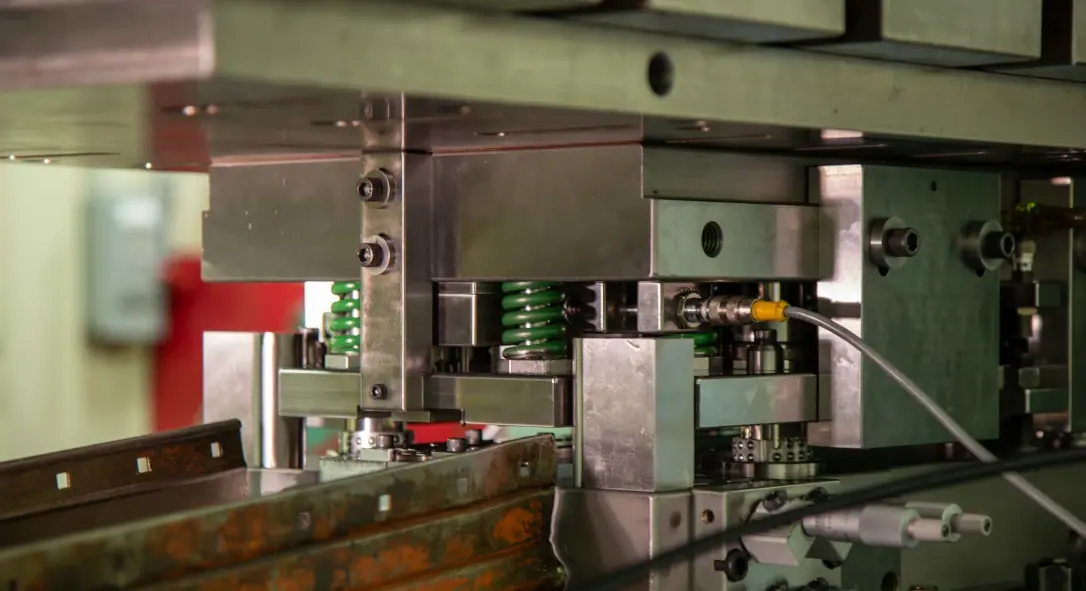