Machining Small Metal Parts: Best Practices & Processes
Machining Small Metal Parts: Best Practices & Processes
Precision is the name of the game in modern manufacturing, especially when it comes to machining small metal parts. Small component manufacturing proves that even the tiniest parts can have a giant impact in aerospace, medical devices, and electronics.
Ensuring reliable, precise parts for a satellite or a microchip isn’t just important—it’s needed for safety measures.
So, what's the secret to mastering how to machine small parts to perfection?
In this article, we’re breaking it all down:
- Why precision matters in small metal parts machining
- Key machining processes
- Best practices
From CNC machining to surface finishing, this article is packed with best practices to ensure success.
Why Precision Matters in Small Metal Parts Machining
The smaller the component, the tighter the tolerances required.
These machining small metal parts often function as:
- Gears
- Fasteners
- Connectors
Even the slightest imperfection can lead to operational failures or safety risks. Given their applications in high-stakes industries, precision is simply non-negotiable.
Here are a few sectors that rely heavily on expertly crafted small metal components:
- Aerospace: Small metal components in engines, sensors, and navigation systems demand aerospace-level precision to maintain safety and performance.
- Medical Devices: From surgical instruments to implantable devices, medical components must meet exact tolerances to comply with strict standards.
- Electronics: Compact, high-performance parts, such as connectors and microchips, keep smartphones, laptops, and other devices functioning seamlessly.
Precision in machining small metal parts directly influences the success of these industries, driving the need for advanced processes and expert practices.
Key Machining Processes for Small Metal Parts
CNC milling involves precision-controlled rotary cutters that remove material to shape the part. It’s ideal for creating intricate geometries and allows for high accuracy and repeatability. Features like pockets, slots, and contours are easily achieved through milling.
CNC turning, on the other hand, is best suited for cylindrical parts such as rods, shafts, and spindles. In this process, the workpiece rotates while a cutting tool removes material.
Some advantages of CNC machining involve:
- Exact and repeatable results.
- Suitable for diverse materials like aluminum, stainless steel, and brass.
- Efficient for both prototypes and high-volume production.
Together, these processes are staples in machining workflows and are known for their speed and consistency.
Electrical Discharge Machining (EDM)
EDM is a noncontact process in which electrical discharges (sparks) remove material from a conductive workpiece. It’s especially suited for machining hard metals or creating fine features that are impossible to achieve with conventional cutting tools.
Types of EDM include:
- Wire EDM: For cutting intricate patterns.
- Sinker EDM: For forming complex molds and cavities.
- Hole EDM: For drilling microholes with extreme precision.
These processes are widely used for aerospace, tool making, and medical equipment to achieve high accuracy in challenging geometries.
Laser Machining
Laser technology's precision and versatility make it a popular option for machining small metal components. Lasers can cut, drill, and engrave without causing material warping, even on highly delicate parts.
Key benefits include:
- Minimal heat-affected zones.
- Exceptional edge quality and precision.
- Ability to work on intricate designs and tiny components.
Laser machining is a prime choice for applications in electronics and medical devices, where every cut must meet strict dimensions.
Best Practices in Machining Small Metal Parts
Selecting the right material is key to achieving machining efficiency and optimal performance for the end product.
Common materials used in machining include:
- Aluminum: Lightweight, corrosion-resistant, and easy to machine, making it a versatile choice for many applications.
- Stainless Steel: Durable and highly resistant to corrosion and wear.
- Brass: Excellent machinability and ideal for electrical or decorative uses.
When choosing a material, it’s important to consider factors such as strength, machinability, and the intended use of the final product to ensure the best results.
Design for Manufacturability (DFM)
The design phase is key in determining machining complexity and overall costs. Following design for manufacturability (DFM) principles, you can streamline production while maintaining high-quality standards.
For instance:
- Avoid overly tight tolerances unless necessary, as these can increase production difficulty and expense.
- Incorporate features that simplify fixturing and alignment to make machining more efficient.
Additionally, minimizing undercuts and complex geometries whenever possible can save time, reduce waste, and lower costs.
Thoughtful design decisions at this stage can dramatically improve both efficiency and product quality.
Tooling and Equipment Maintenance
Proper maintenance of tooling and equipment is necessary for achieving precision and consistency in machining.
Sharp tools are needed, as dull cutting edges can compromise quality and increase machining times. Regular maintenance or replacement of tools ensures smooth operation.
Similarly, CNC machines and other equipment should undergo periodic calibration to maintain their accuracy.
Using the proper coolants and lubricants is equally important, as they reduce heat generation and extend tool life. Consistent upkeep of machinery and tools enhances long-term quality and minimizes unexpected breakdowns.
Resource: Read more about how to extend the lifespan of your tools
with proper maintenance here
Quality Control
Quality assurance is important to the machining process and should be prioritized at every stage.
Doing the following should help maintain consistent quality control:
- Conduct in-process inspections to catch issues early.
- Use precision measurement tools like micrometers and coordinate measuring machines (CMMs) for final verification.
- Document every process to ensure traceability and continuous improvement.
A strong quality control system helps avoid mistakes and builds trust with customers by consistently delivering reliable results.
Surface Finishing Techniques
Proper surface finishing plays a strong role in improving small metal parts' performance, durability, and appearance.
Superfinishing & Plating and Coating
Among the most common and effective techniques is superfinishing, which removes surface irregularities to improve geometry and aesthetics. This process significantly reduces friction, improving the durability of components like gears and bearings and extending their overall lifespan.
Another strong surface finishing method is plating and coating, which improves functionality and visual appeal.
Precision is key when applying uniform finishes to small parts, and a couple of options are widely used based on specific needs:
- Chrome or Nickel Plating: Provides excellent corrosion resistance while enhancing the visual appeal of parts.
- Gold or Silver Plating: Combining functionality with elegance is ideal for high-performance electrical components or decorative applications.
- Black Oxide or Anodizing: Offers robust protection while delivering a unique aesthetic finish. Anodizing is most effective for surface finish on aluminum parts.
This electrochemical process creates a tough oxide layer that increases surface hardness, improves wear resistance, and even allows color customization. It’s a popular choice for applications requiring both durability and design flexibility.
Each technique requires expertise and precision to ensure optimal results, making surface finishing a significant step in metal small component manufacturing.
Best Practices Drive Success
Precision machining small metal parts is not just a technical skill—it’s a vital contributor to industry successes, from the aerospace sector to cutting-edge electronics and life-saving medical devices.
Adopting a methodical approach—from innovative material selection and DFM principles to high-quality machining processes and surface finishing—always ensures exceptional results.
Precision is within reach for those navigating the challenges of making small metal components. Need more help? Contact one of our experts today.
You May Also Like
These Related Stories
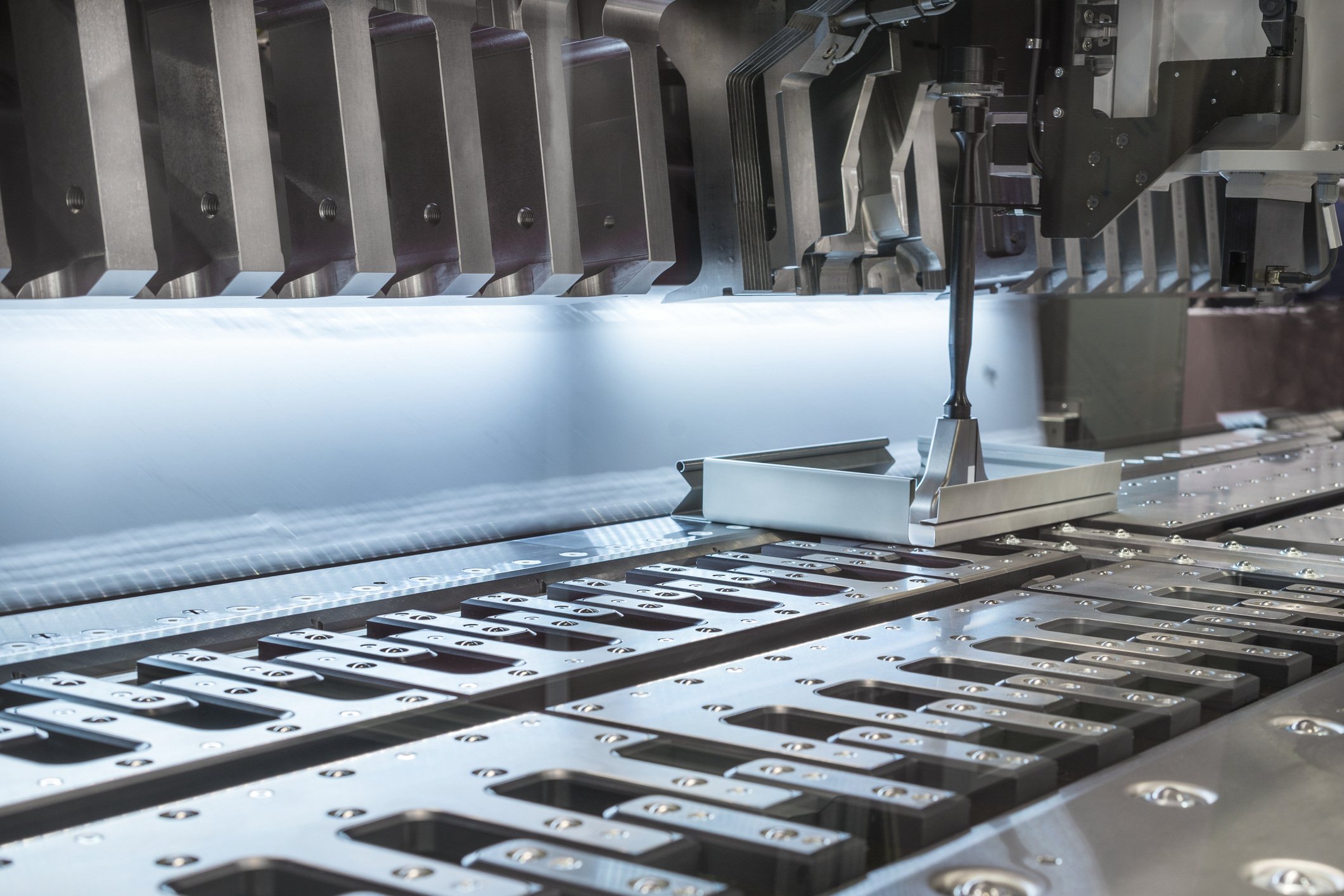
Mastering Tight Metal Stamping Tolerances: A Comprehensive Guide
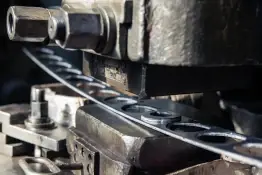
Reducing Manufacturing Lead Time with Progressive Die Stamping
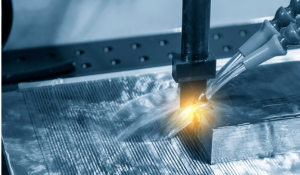