Sheet Metal Stamping Design Guide for Engineers
Sheet metal stamping is a versatile and efficient manufacturing process capable of producing a wide array of complex parts for various industries. However, designing parts for sheet metal stamping requires a specialized understanding of engineering principles and manufacturing limitations.
This comprehensive guide is designed to equip engineers and designers with the knowledge and insights to optimize their sheet metal stamping designs. From material selection and bend considerations to tooling and collaboration with experts, we'll cover every aspect of the process to help you achieve precision, efficiency, and cost-effectiveness in your projects.
Key Considerations for Sheet Metal Stamping Design:
To ensure your sheet metal stamping project is successful, it's essential to consider several critical design factors that can significantly impact the manufacturing process and the final part's quality. Let's explore these key considerations:
1. Material Selection
The choice of material is the foundation of your design. Factors like strength, ductility, formability, corrosion resistance, and cost must be carefully weighed to select the most suitable sheet metal for your specific application. For instance, if your part needs to withstand high stress and wear, stainless steel might be a good choice, while aluminum might be preferable for lightweight applications.
2. Bend Radii and Angles
The radius and angle of bends are crucial for preventing cracks, distortions, and other defects that can compromise the part's integrity. The minimum bend radius is typically determined by the material thickness and type. Sharper bends may be possible with more ductile materials, while thicker materials may require larger bend radii to avoid cracking. Consulting with a stamping expert can help you determine the optimal bend parameters to ensure the part's structural integrity and prevent manufacturing issues.
3. Hole Sizes and Placement
The size and location of holes influence both the functionality and manufacturability of the part. Avoid placing holes too close to edges or bends, as this can weaken the material and lead to distortion during stamping. Additionally, adhere to minimum hole size recommendations based on material thickness to prevent tearing and ensure clean, burr-free holes. Proper hole placement and sizing can streamline the stamping process and improve the overall quality of the part.
4. Flange Design
Flanges provide rigidity and stability to sheet metal parts, but their design can significantly impact the stamping process. Consider factors like flange height, width, and angle to achieve the desired strength and functionality while minimizing material waste. Overly large or complex flange designs can lead to difficulties in forming and may require additional operations, increasing production costs.
5. Tolerances
Clearly defined tolerances are essential for ensuring the part meets its functional requirements and assembles correctly with other components. However, overly tight tolerances can increase manufacturing complexity and cost. It's crucial to understand the capabilities of your stamping provider and work collaboratively to establish realistic tolerances that strike a balance between precision and cost-effectiveness.
Partnering with a Custom Metal Stamping Expert
Collaborating with an experienced metal stamping provider isn't just a choice; it's a strategic decision that can significantly impact the success of your sheet metal stamping project. By partnering with the right expert, you gain access to a wealth of knowledge, experience, and specialized capabilities that can elevate your project to new heights.
Let's explore the compelling benefits of working with a custom metal stamping provider:
1. Improved Part Quality
Custom dies are meticulously designed to match your part geometry, minimizing defects, ensuring consistency, and ultimately delivering superior part quality. The precision of custom dies allows for tighter tolerances, sharper features, and more intricate designs, resulting in parts that meet or exceed your expectations.
2. Increased Production Efficiency
Custom dies are optimized for your specific stamping process, leading to faster cycle times, reduced downtime due to tool changes or adjustments, and increased overall production efficiency. The streamlined workflow enabled by custom dies can significantly boost your production output and reduce manufacturing lead times.
3. Cost Savings
While the initial investment in custom dies may be higher than generic tooling, the long-term cost savings can be substantial. Improved part quality reduces scrap rates and rework, while increased production efficiency translates to lower labor costs and faster turnaround times. Over time, these cost savings can often outweigh the initial investment, making custom dies a wise choice for many applications.
Unlock the Potential of Sheet Metal Stamping:
By following these design guidelines and partnering with a knowledgeable metal stamping provider, you can unlock the full potential of sheet metal stamping for your next project. Whether you need custom metal stamping dies for a complex part or guidance on optimizing your design for manufacturability, working with experts will ensure your project's success.
Ready to take your sheet metal stamping project to the next level? Contact us today to discuss your requirements and get started on your path to precision and efficiency.
You May Also Like
These Related Stories
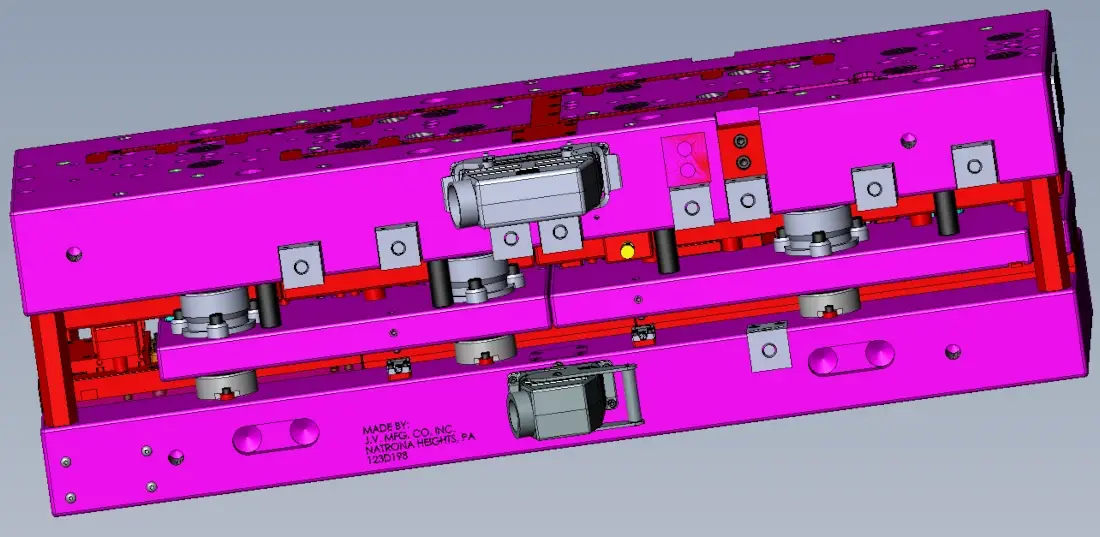
The Engineer's Insights to Progressive Die Design & Innovation
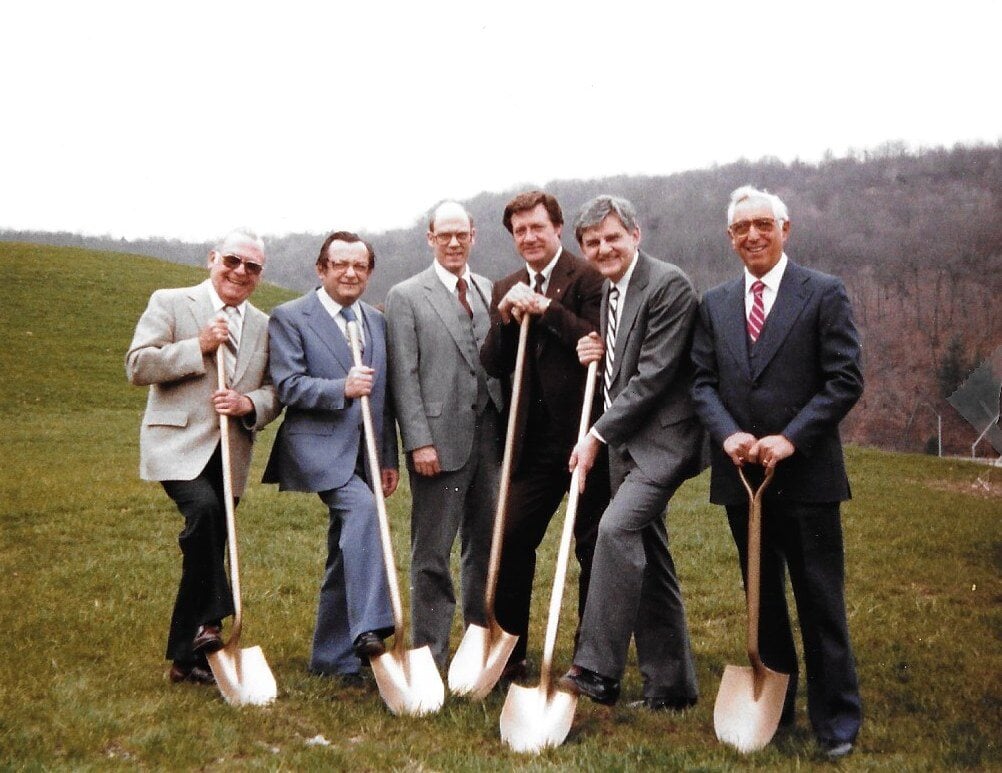
The Story of JV Manufacturing: 50 Years of Excellence
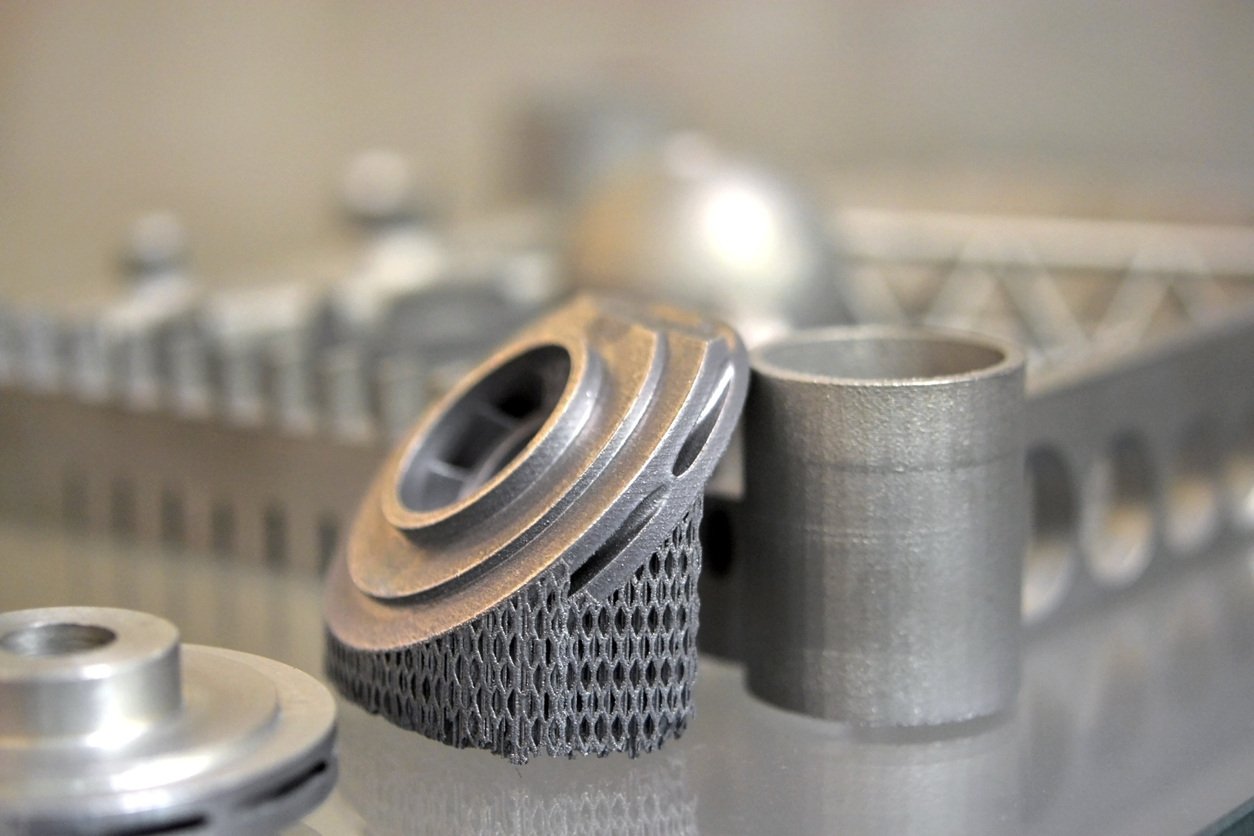