Tool and Die Repair Maintenance
Tired of surprise expenses and production delays? The secret to saving money and boosting efficiency might be in your tool and die maintenance schedule. How’s that?
Through regular tool and die repair and servicing. Essentially upkeep and regular maintenance of both manufacturing elements ensures they’re in good working order and ready to go when you need them.
But just how exactly can you measure the effectiveness of your maintenance? Let’s dig in.
The Case for Regular Tool and Die Repair and Maintenance
For a successful production line, you need an efficient manufacturing process that minimizes interruptions caused by broken tools and dies. To prevent this, well-maintained equipment can reduce the likelihood of unexpected breakdowns, and also prevent costly production halts. With preventative maintenance, you increase the chances of better production. Preventative maintenance schedules enable workers to address any minor issues during planned downtimes rather than during production, to ensure a continuous workflow.
By sticking to a routine maintenance schedule, unexpected issues can be identified and mitigated before they become a serious and expensive problem. Regular inspections, timely sharpening, and proper lubrication ensure that tooling and dies remain in top condition, enhancing their durability. In light of this, you can save money and extend the lifespan of tools and dies through this proactive approach. By extending the life of tools and maximizing their operational efficiency, businesses can avoid the financial burden associated with emergency fixes and downtime, leading to more stable and predictable budgeting for maintenance.
How Do You Maintain a Tool and Die?
Tool and die repair maintenance refers to the regular servicing and upkeep of the tools and dies used in manufacturing processes. These tools and dies are essential for shaping, cutting, forming, and molding various materials into specified designs and dimensions. Maintenance activities can include cleaning, inspection for wear and tear, and lubrication in order to maintain consistent performance and longevity of your tool and die.
Maintaining tooling and dies involves a systematic approach to ensure they operate at peak performance. There are 3 major steps to follow when following key maintenance practices:
- Inspection and monitoring
- Sharpening and Reconditioning
- Alignment and Calibration
1. Inspection and Monitoring
Conduct regular visual inspections to detect any signs of wear, cracks, or damage. Pay close attention to the working surfaces and edges of the tools and dies. In addition to visual inspections, advanced techniques such as ultrasonic testing or magnetic particle inspection are employed. These methods can identify subsurface flaws that are not visible to the naked eye, ensuring comprehensive assessment.
2. Sharpening and Reconditioning
Regularly sharpen and recondition the cutting edges and form features of the tools and dies to maintain the precision and effectiveness of the components. The grinding and honing processes restore the original geometry and sharpness of the tools. These processes help in keeping the desired tolerances and surface finishes.
3. Alignment and Calibration
Alignment is crucial for the accurate operation of tools and dies. Regularly check and adjust the alignment to prevent any operational inconsistencies that could impact the quality of the final product. Calibrate the tools and dies to ensure optimal pressure and force distribution. Proper calibration helps in achieving uniform performance and prolonging the life of the equipment.
Importance of Using Appropriate Shims and Lubrication
The application of correct shims and lubrication is an important step in maintenance. This aids in both the performance and longevity of the equipment.
Shims are components that help make sure there is enough space and positional accuracy. They play a key role in adjusting clearances and alignments, making certain that the tools and dies operate seamlessly.
Using the appropriate shims minimizes the risk of any misalignment. If not, this can lead to:
- uneven wear
- material deformation
- and possible damage to the dies and products being manufactured.
Therefore, selecting the right type and thickness of shims tailored to specific requirements is major for maintaining operational consistency.
Proper lubrication is just as equally important in making sure there is a smooth operation of all moving parts within the tool and die maintenance. Lubrication reduces friction between surfaces, preventing excessive heat generation that could lead to material fatigue and failure. It also helps in protecting against corrosion and the infiltration of any harmful elements. Without lubricating, this can significantly impair the functionality of the dies. There are different types of lubrications to minimize friction, such as oils and greases, to suit different operational conditions and material compatibilities.
Type of Lubrication |
Description |
Key Applications |
Oil Lubrication |
Includes mineral and synthetic oils, providing versatility and high performance under various conditions. |
Used in engines, machinery, and hydraulic systems. |
Grease |
Varieties such as lithium and calcium grease offer specific properties like temperature tolerance and water resistance. |
Suitable for bearings, joints, and other applications where liquid lubricants are impractical. |
Solid Lubricants |
Includes graphite and molybdenum disulfide, effective in high-temperature and high-pressure environments. |
Used in extreme conditions, such as aerospace and heavy industrial applications. |
Penetrating Lubricants |
Low-viscosity oils that can penetrate tight spaces to loosen rusted parts and provide protection against corrosion. |
Ideal for freeing stuck bolts and nuts, and for general maintenance. |
Dry Lubricants |
Non-oily lubricants like PTFE are used where grease or oil is unsuitable. |
Common in electrical applications and where contamination from oil is a concern. |
Bio-based Lubricants |
Made from renewable resources, these lubricants are environmentally friendly and biodegradable. |
Increasingly used in industries focusing on sustainability, such as agricultural machinery. |
Read more here about how to properly assemble your dies
The High Cost of No Maintenance
Poorly maintained tools and dies can severely impact the quality and efficiency of production processes. As wear and misalignment issues go unaddressed, the precision and consistency of the output can decrease, leading to lower-quality products that fail to meet industry standards or customer specifications. Slowdowns due to constant readjustments and fixes can also hinder production rates, affecting overall productivity. This decline in product quality and manufacturing speed inevitably leads to customer dissatisfaction, potentially harming the company's reputation and resulting in lost business.
Safety is the #1 concern in any manufacturing environment, and poorly maintained equipment significantly increases the potential risk of workplace accidents and injuries. Malfunctioning tools and dies can cause operational hazards, such as unexpected machinery stops, and ejections of materials, which all put workers at risk.
Best Practices: Preventative Tool and Die Maintenance
For optimal performance and longevity of your tool and die equipment, following a set of essential steps for tool and die repair will make sure there are consistent best practices. Following these steps can help establish an effective maintenance routine:
- Establish a scheduled maintenance program
- Implement predictive maintenance
- Train staff on maintenance best practices
- Select an experienced service provider
1. Establishing a Scheduled Maintenance Program
A structured maintenance program is the foundation of effective tool and die upkeep. Establishing a detailed schedule for routine inspections, cleaning, lubricating, and sharpening guarantees that all aspects of the equipment are regularly attended to.
2. Implementing Predictive Maintenance
Predictive maintenance techniques go beyond the traditional approaches by using advanced technologies to predict potential failures before they occur. Methods such as vibration analysis, thermal imaging, and acoustic monitoring can detect abnormalities that indicate any wear or malfunctions for tool and die repair.
3. Training Staff on Maintenance Best Practices
Proper training of staff makes sure tools and dies are handled and maintained correctly. Providing comprehensive training on inspection procedures, lubrication techniques, alignment, calibration, and the use of predictive maintenance tools is important. This training can equip employees to perform routine maintenance tasks effectively. Skilled staff can identify and address potential issues swiftly, promoting a culture of proactive maintenance and operational excellence.
4. Select an Experienced Service Provider
When outsourcing tool and die maintenance, it goes without saying to partner with a service provider with expertise in the field. Ideally, the provider should have years of experience in manufacturing tooling and dies, as this makes sure there is a deep understanding of the equipment's details and maintenance requirements. An experienced supplier will offer tailored maintenance solutions, ensuring high-quality service that maximizes the performance and longevity of the tools and dies.
Need more help? We have your back, learn more about our other services here
Don't Let Your Tools Retire Early: Unlock the Power of Expert Maintenance
Don’t let your operations be hampered by avoidable breakdowns or mediocre outcomes. Commit to a strong maintenance strategy today to secure the endurance and efficiency of your tools and dies. Stay ahead of the competition by achieving reliable consistency in your manufacturing process.
Ready to level up your manufacturing game?
Get in touch with us today for expert maintenance solutions tailored to your needs.
You May Also Like
These Related Stories
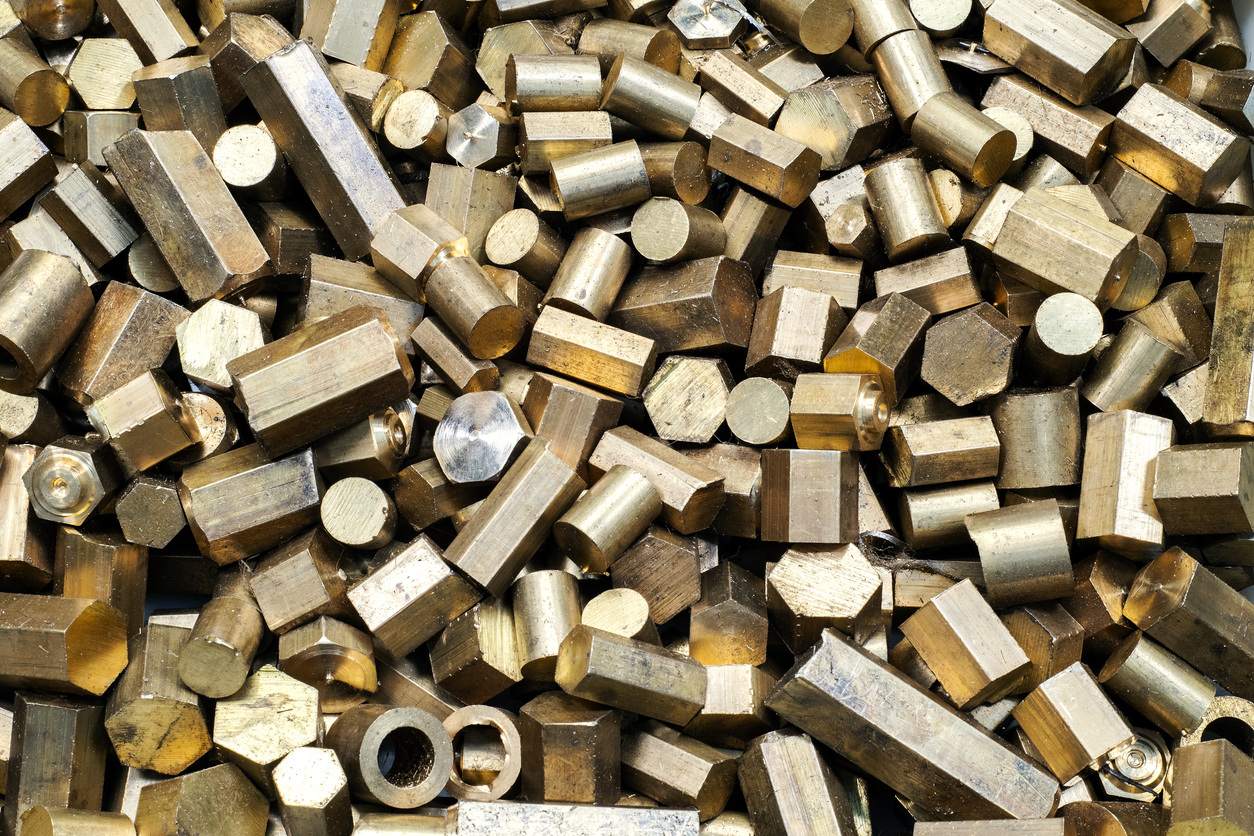
Die Steel Material Choices That Shape Progressive Stamping

Machining Small Metal Parts: Best Practices & Processes
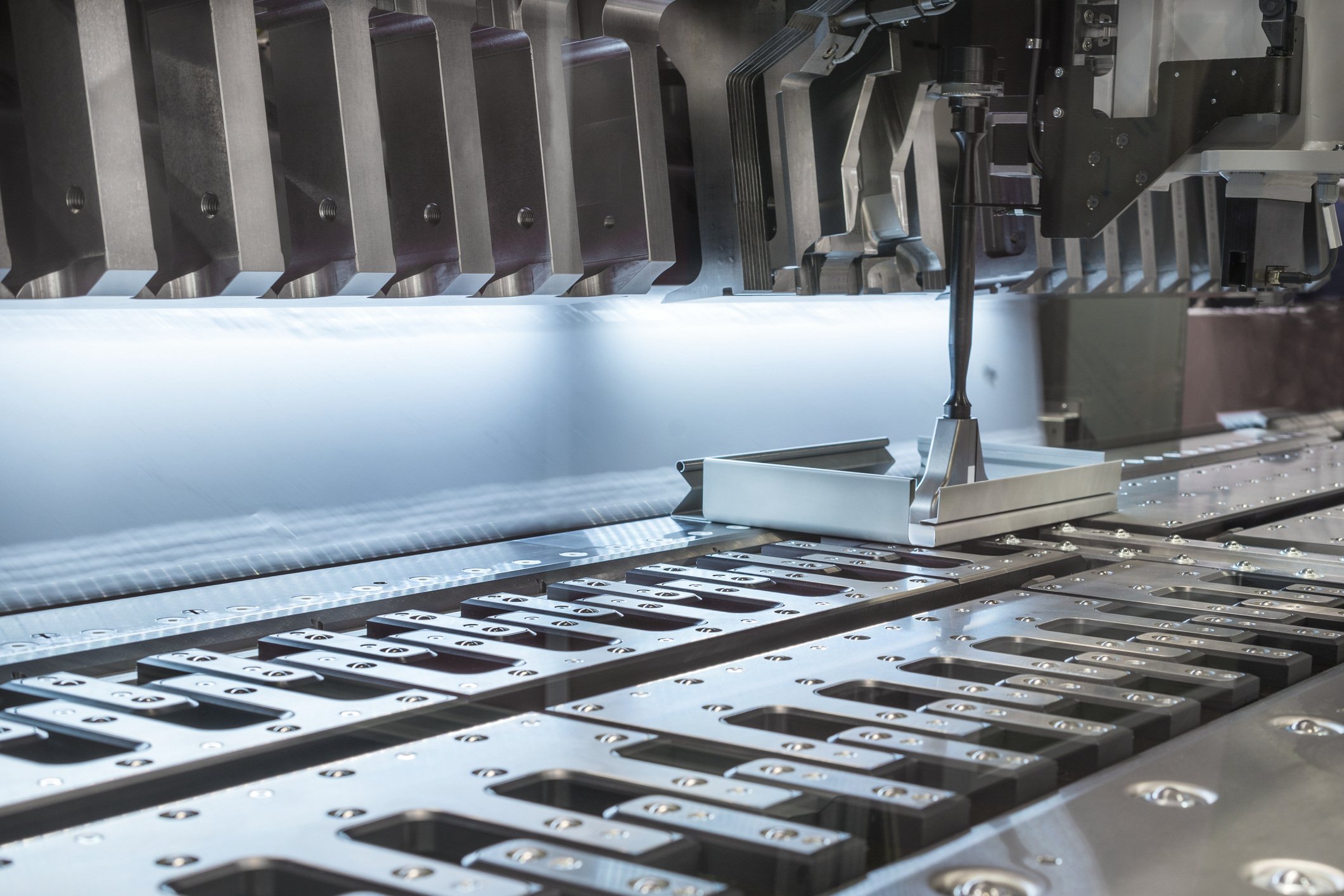