Understanding Quality Assurance in Progressive Metal Stamping
Quality assurance is the heartbeat of the metal stamping process, making sure every part meets the highest standards of precision and reliability. As industries demand flawless components, the role of quality control has never been more critical.
Progressive metal stamping blends speed with accuracy.
But the strict quality checks behind the scenes truly set top-tier manufacturers apart.
From the moment raw materials enter the production line, every step is carefully monitored, measured, and inspected. Advanced technologies catch defects early, while routine equipment calibration ensures perfect execution with every press.
Partnering with a metal stamping manufacturer that adheres to ISO 9001 standards ensures consistent quality while minimizing costs.
Quality Assurance in Metal Stamping: A Brief Overview
Quality assurance in metal stamping is an organized approach to assuring that products meet specific quality and performance standards. It involves implementing processes and procedures to minimize defects and maximize stamped metal components' reliability and durability. Quality assurance involves three main stages, including:
- Prefabrication inspections
- Production monitoring
- Post fabrication testing
Each stage ensures that every aspect of the metal stamping process adheres to predefined quality benchmarks. The scope of quality assurance in metal stamping extends to evaluating equipment efficiency and personnel's skill level, thereby providing an effort to produce high-quality outcomes.
ISO standards are key to know in quality assurance within the metal stamping industry. These international standards provide a framework for establishing a consistent and high-quality production process. By adhering to ISO standards, metal stamping companies can guarantee that their products comply with global quality requirements, improving consumer trust and market competitiveness.
ISO certifications, such as ISO 9001, focus on quality management systems. They require stringent auditing and continuous improvement, which help identify inefficiencies and set clear guidelines for quality objectives in the progressive die stamping process. By adopting ISO standards, manufacturers can achieve operational excellence and maintain a strong quality assurance system.
1. Prefabrication Inspections
Prefabrication inspections are important in any metal stamping process, especially in progressive die stamping. They aim to detect and fix any potential issues before production begins. This stage of quality assurance in metal stamping contributes to the quality and reproducibility of metal-stamped products by precisely examining materials, equipment, and processes before production.
By addressing these areas, prefabrication inspections help prevent costly rework, reduce material waste, and maintain a consistent quality output throughout manufacturing.
Prefabrication inspections also identify and correct defects and inconsistencies early in the progressive die stamping cycle, minimizing the risk of defects and inconsistencies in the final output. This proactive approach results in a more stable and predictable production process, allowing manufacturers to deliver products that consistently meet or exceed quality stamping and machining standards.
Through improved documentation and process control, pre-fabrication inspections facilitate continuous improvement, supporting long-term operational excellence and market competitiveness.
Key Inspection Techniques and Technologies
Several key techniques and technologies provide precision and accuracy during pre-fabrication inspections. These advanced methods include:
- Non-destructive testing (NDT): This technique assesses the properties of a material, component, or system without causing damage, ensuring safety and reliability in various industries such as aerospace and manufacturing.
- Coordinate measuring machines (CMM): CMMs measure the geometry of physical objects by sensing discrete points on the surface, providing precise measurements for quality control and inspection.
- Laser scanning: This technology uses laser beams to capture detailed information about an object's shape and position, creating accurate 3D models for applications in construction, archaeology, and more.
- CAD (Computer-Aided Design) models: Visual inspections and verifications are also integral, providing a clear comparison against design blueprints. CAD models allow for quick and accurate checks of dimensions, tolerances, and other critical design features.
These technologies evaluate material properties and geometric conformity without causing damage.
Moreover, including automation and digital imaging technologies for quality assurance in the metal stamping process helps increase the speed and reliability of inspections, thereby improving overall production efficiency.
2. Production Monitoring
During fabrication, careful monitoring and control techniques are important to upholding quality stamping and machining standards and optimizing operational efficiency.
Key techniques involve:
- Real-time data acquisition systems: This technique tracks and analyzes production metrics, allowing for swift identification and correction of anomalies.
- Automated feedback loops: This technique enable precise adjustments to be made instantly to maintain process integrity and prevent deviations.
- Statistical process control (SPC): This technique involves sampling and analyzing data to predict trends and ensure parameters remain within predefined limits.
Proactive measurements help control variables during fabrication and enhance product quality by reducing variability and preventing defects. These processes provide the consistent capability to deliver reliable, high-quality metal components aligned with stringent quality assurance goals by ISO Standards.
ISO Standards in Fabrication Processes
Implementing ISO standards is required in fabrication processes, holding a commitment to quality and reliability.
ISO 9001:2015 certification proves dedication to a comprehensive quality management system focused on continuous improvement and customer satisfaction. This standard provides a structured framework guiding operations, ensuring consistency in delivering high-quality parts.
Adhering to these internationally recognized standards streamlines processes improves efficiencies, and enhances performance, underscoring a commitment to excellence in the metal stamping industry.
Resource: Explore JV Manufacturing, an ISO 9001 certified company, here
This compliance enhances global competitiveness and customer confidence by delivering products that meet international quality requirements. Manufacturers can continuously demonstrate their capability to uphold quality assurance principles through standardized testing procedures.
3. Post-Fabrication Testing
Post-fabrication testing is required to verify the quality and integrity of stamped metal products before they are released into the market. Testing ensures the final products meet predetermined quality standards and function optimally within their intended applications.
Common tests include:
- Mechanical tests: These tests involve tensile and hardness tests, assessing a material's strength and durability.
- Corrosion testing: This evaluates the material's resistance to environmental factors, while dimensional inspections verify that components meet precise measurements and tolerances.
- Non-destructive testing (NDT): This involves ultrasonic or radiographic testing and is also employed to identify internal defects without damaging the components.
Proper testing provides comprehensive quality assurance and ensures only products meeting the highest standards are shipped to customers.
Ensuring Quality Assurance in Metal Stamping Every Step of the Way
Partnering with a quality-driven progressive metal stamping expert ensures your products consistently meet the highest standards. With meticulous quality assurance processes, such as rigorous inspections, advanced measurement technologies, and compliance with ISO standards, your production achieves the reliability and precision required in today’s market.
Ready to Elevate Your Quality Standards?
Contact us today to learn how our quality assurance processes in progressive metal stamping can elevate your production, ensuring precision and consistency at every stage. Let us help you navigate the complexities of quality control with tailored solutions that protect your products and strengthen your brand in the marketplace.
You May Also Like
These Related Stories
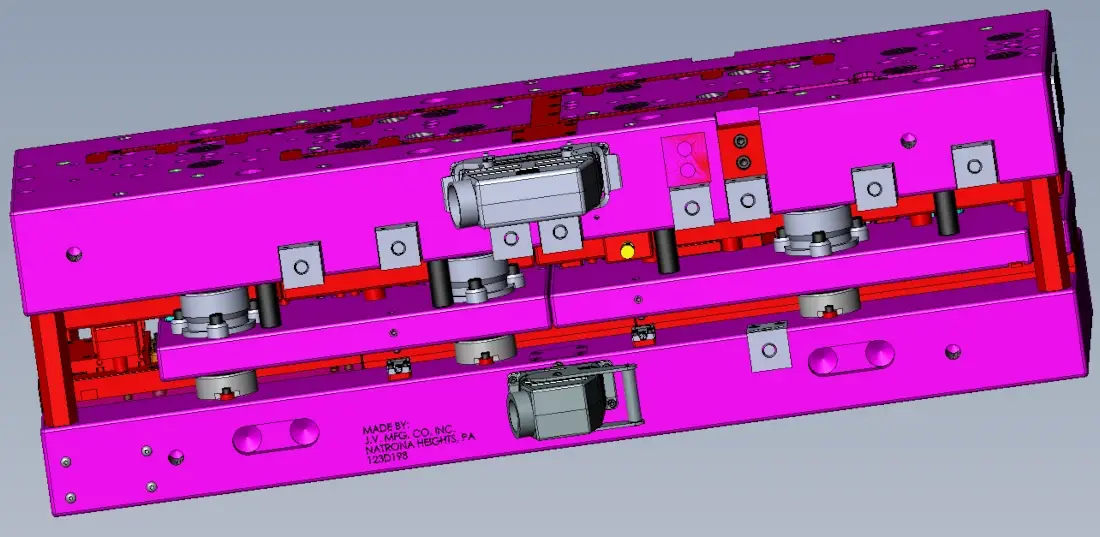
The Engineer's Insights to Progressive Die Design & Innovation
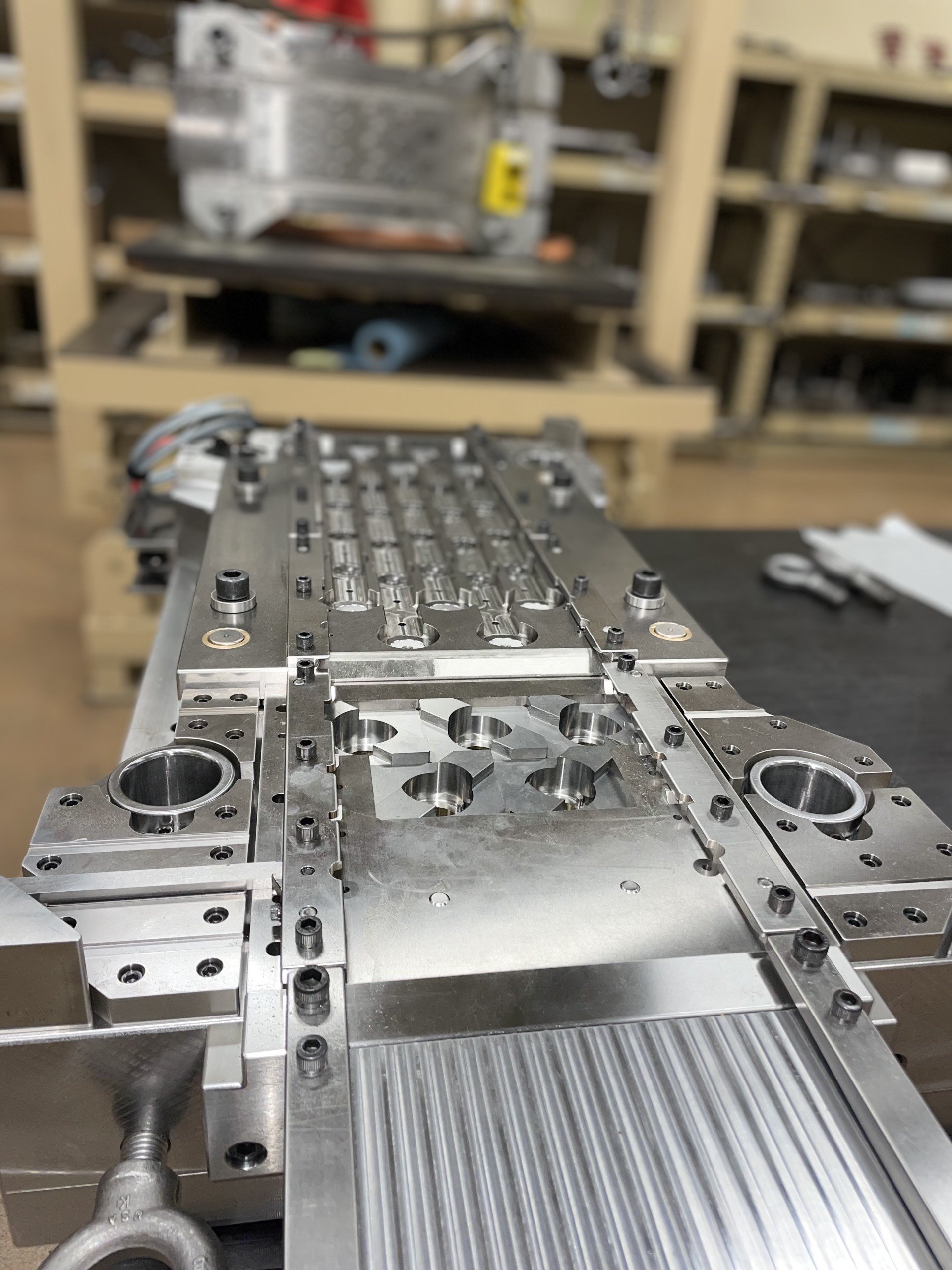
Progressive Die Stamping: An Overview
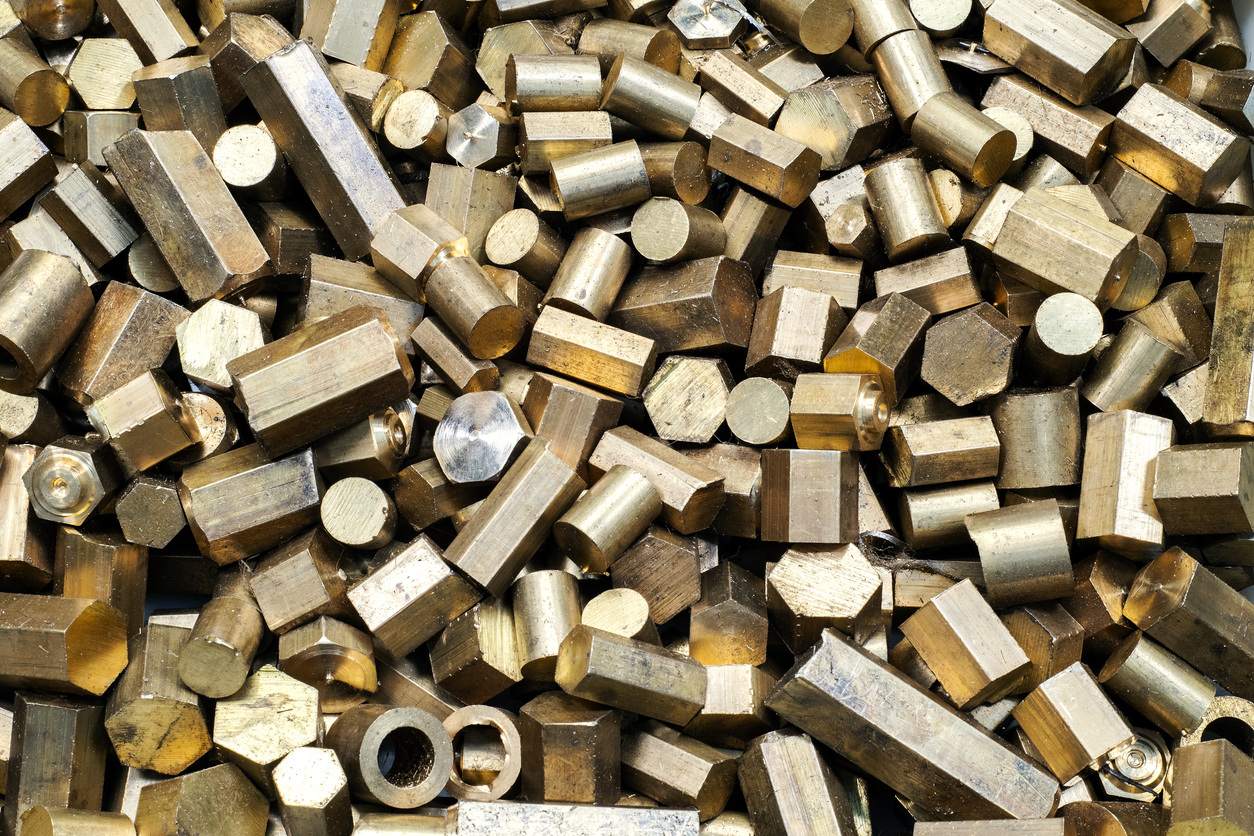