Using the Electrochemical Machining Process for the Aerospace Industry
Do you enjoy the struggle of machining complex geometries with conventional machining methods?
Neither do we. We turn to electrochemical machining (ECM) for precision and efficiency.
If you’re reading this, you likely understand that ECM offers strategic advantages in producing intricate components with high precision and superior surface finishes. This advanced technology improves engine performance and meets the stringent standards required in defense projects and modern aerospace applications.
Whether considering ECM for the first time or re-evaluating its potential against conventional methods, it’s crucial to understand the significant advantages ECM provides. Traditional processes may not fully capture the intricate designs and materials necessary for aerospace components.
But here’s what you need to know: ECM is more than just an alternative—it’s a transformative approach.
This article will reveal key factors to help you decide if ECM is right for elevating your production capabilities and meeting the demands of the aerospace industry.
Electrochemical Machining Process in the Aerospace Industry | Brief Overview
Electrochemical machining leverages the principles of electrochemistry to remove metal by anodic dissolution without contact and wear between the tool and the workpiece. This non-traditional machining method is ideally best for producing intricate parts with high precision and fine surface finish.
The aerospace industry demands components that are lightweight and high-strength and manufactured with exacting precision. ECM is beneficial for machining superalloys, titanium, and other materials that exhibit toughness and heat resistance, which are common in aerospace applications.
By using ECM, manufacturers can achieve complex geometries and critical tolerances required for high-performance parts such as turbine blades, blisks, and fuel system components, ensuring reliability and efficiency in aerospace operations.
Reducing Time to Market: The 3 Benefits of ECM in Aerospace
The primary challenge in machining aerospace materials lies in their toughness and heat resistance, which make them difficult to cut using conventional methods such as Wire Electrical Discharge Machining (WEDM) or milling.
The three beneficial methods of electrochemical machining include:
- Reduced production times
- Efficiency with hard-to-machine materials
- Improved precision and surface finish
1. Reduced Production Times
One of the most compelling advantages of ECM in aerospace manufacturing is its impact on reducing production times.
By replacing Wire Electrical Discharge Machining (WEDM) and milling with ECM, companies in the aerospace sector can increase throughput, reduce cycle times, and streamline workflows while maintaining the highest standards of quality and structural integrity critical in aerospace components.
This shift improves production efficiency and contributes to faster delivery times, which is invaluable in meeting the fast-paced demands of the aerospace industry.
2. Efficiency With Hard to Machine Materials
Traditional machining methods, such as WEDM and milling, can be time-consuming due to their dependence on mechanical removal processes that involve significant physical contact and resultant tool wear and tear. These methods often struggle with hard-to-machine materials, leading to longer production cycles and increased tool replacement costs.
ECM operates through an electrochemical process that removes material without direct contact. This eliminates the downtime associated with tool wear and the need for frequent tool changes, dramatically speeding up the machining process.
3. Improved Precision and Surface Finish
ECM also provides exceptional precision and surface finish in a single operation, which minimizes the need for secondary finishing procedures that would otherwise extend lead times.
ECM's accuracy and repetitiveness mean that manufacturers can achieve desired tolerances and specifications immediately without the constant adjustments often required with mechanical techniques.
Types of Materials Used in ECM for Enhanced Effectiveness
The non-contact nature of electrochemical machining makes it particularly adept at handling various materials commonly found in aerospace engineering. Its non-contact nature and precision capabilities make it especially suitable for materials challenging to the machine through traditional methods. Some of the key materials include:
- Nickel-based Superalloys: Due to their exceptional high-temperature strength, corrosion resistance, and durability, they are a staple in aerospace engineering, particularly for turbine engine components. ECM effectively machines these challenging materials without inducing thermal stresses or material degradation.
- Titanium Alloys: This material is needed in aerospace designs because of their high strength-to-weight ratios and resistance to extreme temperatures. ECM's ability to shape titanium precisely without mechanical stress or tool wear is a significant advantage for producing components like airframe structures and engine parts.
- Stainless Steel: Frequently used in aerospace applications for its robust mechanical properties and corrosion resistance, stainless steel benefits from ECM for achieving smooth finishes and precise dimensions, which are necessary for components requiring exact fit and performance.
Recent innovations in material science have expanded the range of ECM-compatible materials, improving its effectiveness in aerospace applications:
- Conductive Ceramics and Composites: These materials combine the strength and heat resistance required in aerospace with electrical conductivity essential for ECM. ECM enables the machining of detailed shapes in conductive ceramics and composite materials while maintaining superior structural integrity.
- Copper and its Alloys: Valued for excellent thermal and electrical conductivities, copper and its alloys are also machined efficiently through ECM. It facilitates the creation of complex shapes and fine surfaces in these alloys used in aerospace electrical systems and heat exchangers.
Through these advancements, ECM continues to push the boundaries of what is possible in aerospace manufacturing, allowing for the precise and efficient production of components made from cutting-edge materials.
Electrochemical Machining Applications
In the aerospace industry, electrochemical machining helps create complex, high strength parts in multiple sectors. The following sectors where ECM serves a significant role in aerospace include:
Engine Components
Engine parts such as compressor blades and combustion chambers require high precision and complex geometries to function effectively.
ECM's ability to produce these shapes with exceptional accuracy and fine surface finishes ensures optimal aerodynamics and fuel efficiency, directly contributing to enhanced engine performance. The non-contact nature of ECM eliminates tool wear and minimizes the introduction of micro imperfections, which could otherwise affect the performance and longevity of these components.
Defense Projects
In defense projects, where the demand for reliability and precision is paramount, ECM stands out for its capability to manufacture intricate components with high precision.
Defense aircraft often require components with complex geometries and high-strength materials to withstand extreme conditions. ECM facilitates the production of parts with critical tolerances and superior surface quality, ensuring they meet the rigorous standards required for defense applications.
The process allows for the creation of lightweight, durable parts essential for advanced defense systems, ensuring enhanced performance and operational safety.
Fan Blades and Blisks
ECM's application in producing fan blades and blisks shows its capacity for handling high-performance engine components. These elements are crucial for maximizing thrust and reducing fuel consumption in modern aerospace engines.
ECM enables the precise machining of these components from high-strength materials like titanium and superalloys, which traditional methods find challenging. The ability to create complex features such as cooling passages and aerodynamic profiles in a single, clean operation ensures engine efficiency while maintaining structural integrity.
This capability is invaluable in meeting the advanced requirements of high-performance aerospace engines, driving improvements in speed, fuel economy, and overall engine life.
Case Study of Turbine Disks for GE and Rolls Royce
With the need for high precision and quality in turbine disks, GE and Rolls Royce transitioned from traditional machining methods to ECM.
This shift significantly reduced production time and ensured the components' reliability and longevity. ECM's non-contact and stress-free machining capabilities allowed for creating complex geometries and superior surface finishes, surpassing traditional methods.
The collaboration between GE and Rolls Royce has been key in exploring ECM's potential and achieving substantial improvements in production efficiency and alignment with stringent aerospace standards.
Advancing Aerospace Excellence: The Value of Electrochemical Machining Partnerships
Partnering with an expert in electrochemical machining delivers strategic benefits, such as achieving the high precision and complex geometries required in aerospace manufacturing. Selecting an ECM specialist prioritizes the quality and reliability of your engine components, fan blades, and defense projects, all while enhancing production efficiency.
Ready to Elevate Your Aerospace Manufacturing?
Contact us today to discover how ECM can transform your production process and ensure your components meet the highest performance and quality standards. Let us help you navigate the complexities of advanced manufacturing with tailored ECM solutions that drive efficiency and innovation.
You May Also Like
These Related Stories
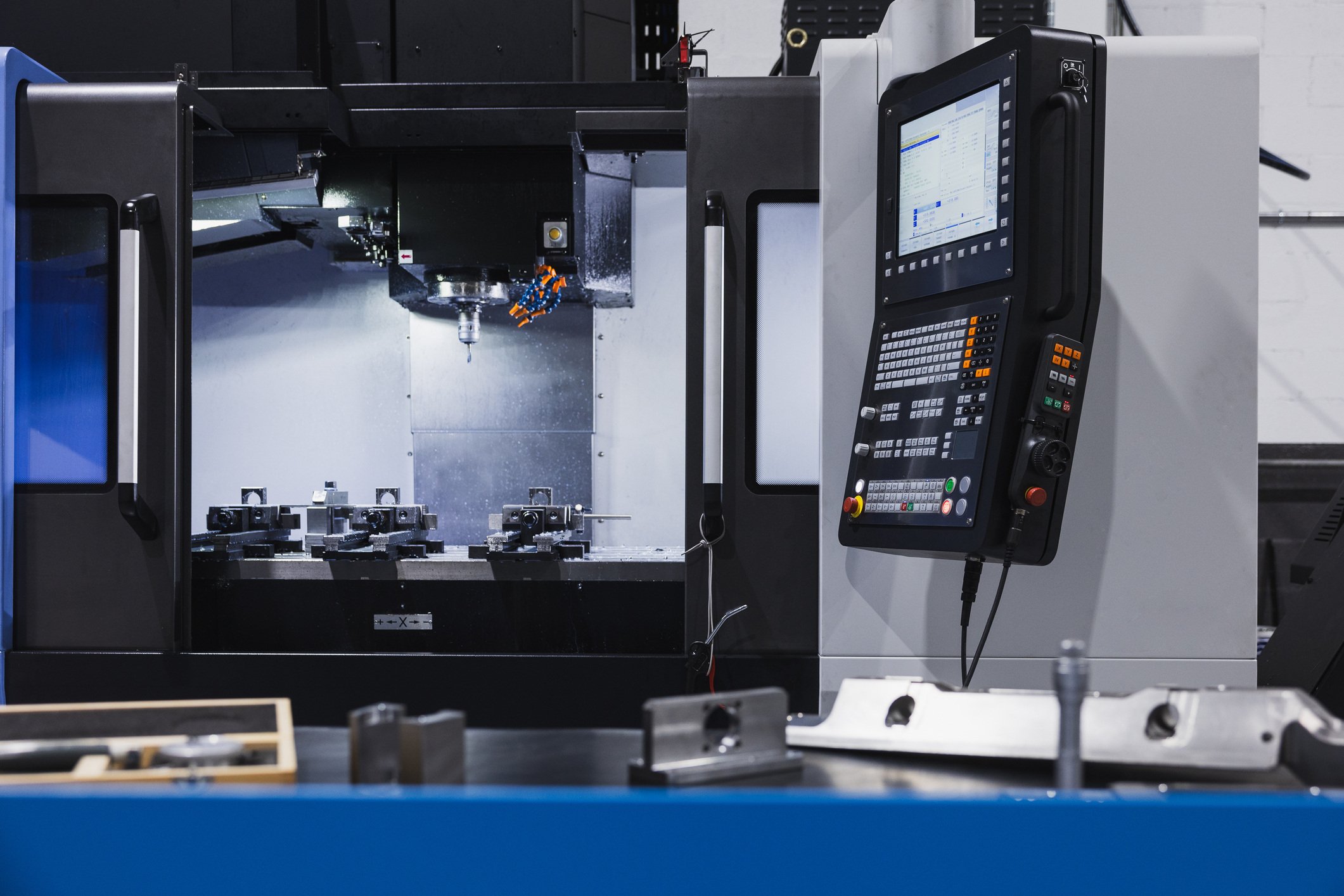
Machining Vs. Casting: Key Differences, Advantages, & Applications
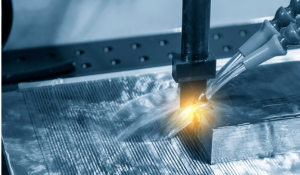
ECM Vs. EDM Machining: What’s the Difference?
