Plastic Stamping for Industrial Applications
Driven by its ability to efficiently produce high-quality plastic parts at a remarkable pace, plastic stamping is flourishing in the manufacturing sector.
In 2023, the global plastic market was valued at approximately USD 624.8 billion. It is projected to expand at a compound annual growth rate (CAGR) of 4.2% from 2024 to 2030.
Industry leaders expect this trend to continue, reinforcing plastic stamping's role as a staple in mass production. Precision tooling technology has been essential in this evolution, allowing for the rapid creation of complex plastic components across various industries.
Plastic stamping in modern manufacturing has changed the game of producing plastic products in manufacturing. As it is highly efficient, it is also an environmentally friendly option to produce plastic compared to other plastic stamping manufacturer processes that produce excess waste.
The Mechanics of Plastic Stamping
It might seem odd that plastic can have the same treatment as metal, but advancements in precision tooling and technology have made it possible. The outcome is a reliable method for mass-producing intricate plastic components that meet stringent industry standards.
The plastic stamping process involves placing a sheet or film of plastic between two dies. One die forms the workpiece into the desired shape, while the other die acts as a counterforce. The dies then press together with high force onto the plastic forming the desired shape. This can either be a cold or hot press depending on the plastic material's properties.
Different types of dies are used based on the complexity and specifications of the project. The two most common types of dies include:
- Compound Dies: These are the most commonly used in plastic stamping, as they allow for multiple operations to be performed in one press stroke. They consist of two or more stations that perform different actions on the plastic sheet.
- Progressive Dies: These dies are used for high-volume production and involve feeding the plastic sheet through a series of stations, with each station
Machines and Technology Employed in Plastic Stamping
Plastic stamping machines vary in size and complexity, largely depending on the type of die used and the requirements of the final product. However, they all function similarly by applying high pressure to the dies to form the plastic into a specific shape.
Plastic stampers frequently use:
- Punch presses: These machines are specifically designed for plastic stamping and allow for high precision and speed in the process. They come in various sizes and strengths, catering to different production needs.
- High-speed options: To keep up with the demand for faster production, high-speed plastic stamping machines have been developed. These machines use advanced technology such as servo motors.
Resource: Discover how our reliable services stamp offers accuracy here
Overview of the Process and Materials Used
Dies used for plastic stamping are made of hardened steel or other durable materials that withstand high pressure and repeated use. As for the plastic material, it can vary depending on the application and required properties of the final product:
- Vulcanized Fibers: This material is heat and moisture-resistant, making it suitable for electrical insulation components.
- Thermoplastics: These include materials such as PVC, PET, and ABS. They are flexible and can be molded into various shapes easily.
- Thermoset Plastics: Unlike thermoplastics, these materials cannot be recycled or remolded. This is because they undergo a chemical reaction that permanently sets them as the desired shape. However, they possess durability properties that make them suitable for applications requiring resistance to heat and chemicals.
- Laminates: Used in various industrial and consumer applications, these are made by bonding multiple layers of plastic sheets together to enhance strength and durability.
Plastic Stamping Advantages and Disadvantages
As a fabrication process that has its place in many industries and creates a wide variety of components, plastic stamping has benefits that are hard to ignore. Still, there are some downfalls to this component-creation process that are worth consideration well before committing to this production method. Let's look at both.
Advantages
- Cost-efficiency and High Production Speed
Once the initial setup and tooling are complete, the plastic stamping allows for the rapid production of large quantities of parts. This is particularly advantageous for industries such as automotive and consumer goods, where large-scale production is often required to meet market demands. - Versatility in Materials and Product Design
The plastic stamping process is compatible with a wide range of materials, including various grades of thermoplastics and composites. This versatility gives manufacturers more leeway in selecting the most appropriate material for the application against considerations such as:
- Strength
- Flexibility
- Durability
Additionally, the stamping process can accommodate a variety of designs from simple flat pieces to more complex geometries, making it a flexible option for diverse product requirements.
Disadvantages
- Limitations in Material Thickness and Part Complexity
While plastic stamping is versatile, it does have limitations concerning the thickness of the materials used and the complexity of the parts produced. Thicker materials can be challenging to stamp effectively, which may limit the process to thinner sheets, affecting the durability and application of the finished product. Additionally, highly complex part designs may not be achievable or may require multiple processing steps, potentially increasing costs and production time. - Challenges in Maintaining Precision with Intricate Designs
Maintaining precision in intricate designs is a significant challenge in plastic stamping. The finer details of a design may not always be accurately replicated, especially when working with softer plastics that may warp or deform under pressure. This can lead to a higher rate of defects and waste, particularly in designs requiring high tolerances and strict dimensional accuracy. To mitigate these issues, manufacturers may need to invest in higher-quality tooling or modify the design to suit the stamping process.
Category |
Advantages |
Disadvantages |
Production Efficiency |
Cost-efficiency and high production speed after initial setup. Ideal for large-scale production. |
Limitations in material thickness and part complexity can increase costs and production time for more complex designs. |
Material and Design |
Versatile in material selection (various thermoplastics and composites) and product design. |
Challenges in maintaining precision with intricate designs, lead to possible defects and waste. |
Flexibility |
Can accommodate simple to complex geometries, enhancing product customization. |
Thicker materials are difficult to stamp, restricting use to thinner sheets which might affect durability and application. |
Application Suitability |
Suitable for industries like automotive and consumer goods that require rapid, large-scale production. |
Highly complex designs may require adjustments or multiple processing steps, potentially compromising efficiency. |
Plastic Stamping: Merging Efficiency & Versatility
Plastic stamping offers streamlined production capabilities and flexibility in design. With the ability to quickly produce large volumes, this method is ideal for industries requiring rapid turnaround and consistent quality.
With the right approach, plastic stamping can be a powerful asset in your manufacturing toolbox.
Ready to Dive Deeper?
Discover more insights and strategies on industrial stamping processes at our blog.
You May Also Like
These Related Stories
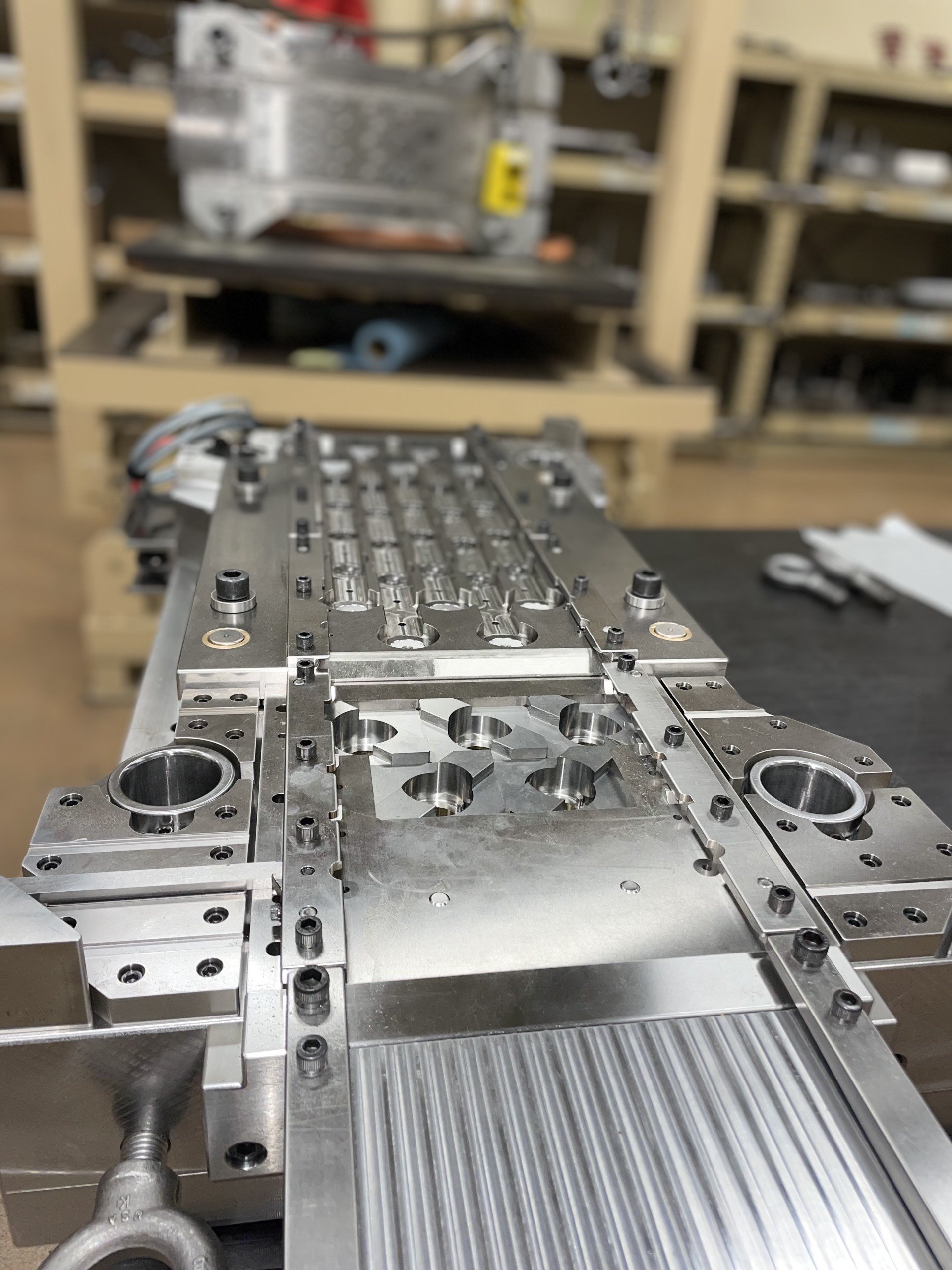
Progressive Die Stamping: An Overview
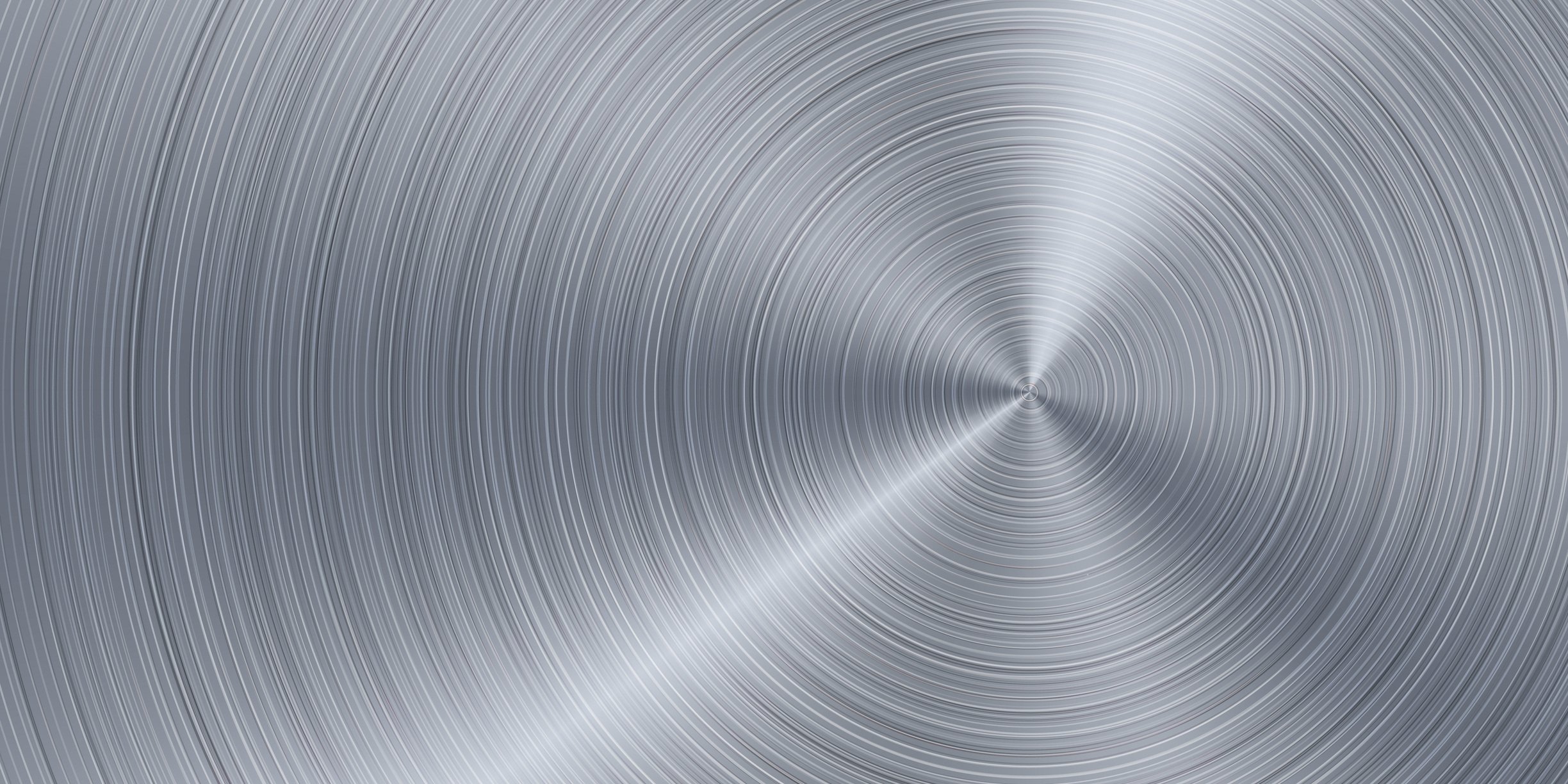
Types of Sheet Metal Finishing: Choosing the Right Process for Strength & Appearance
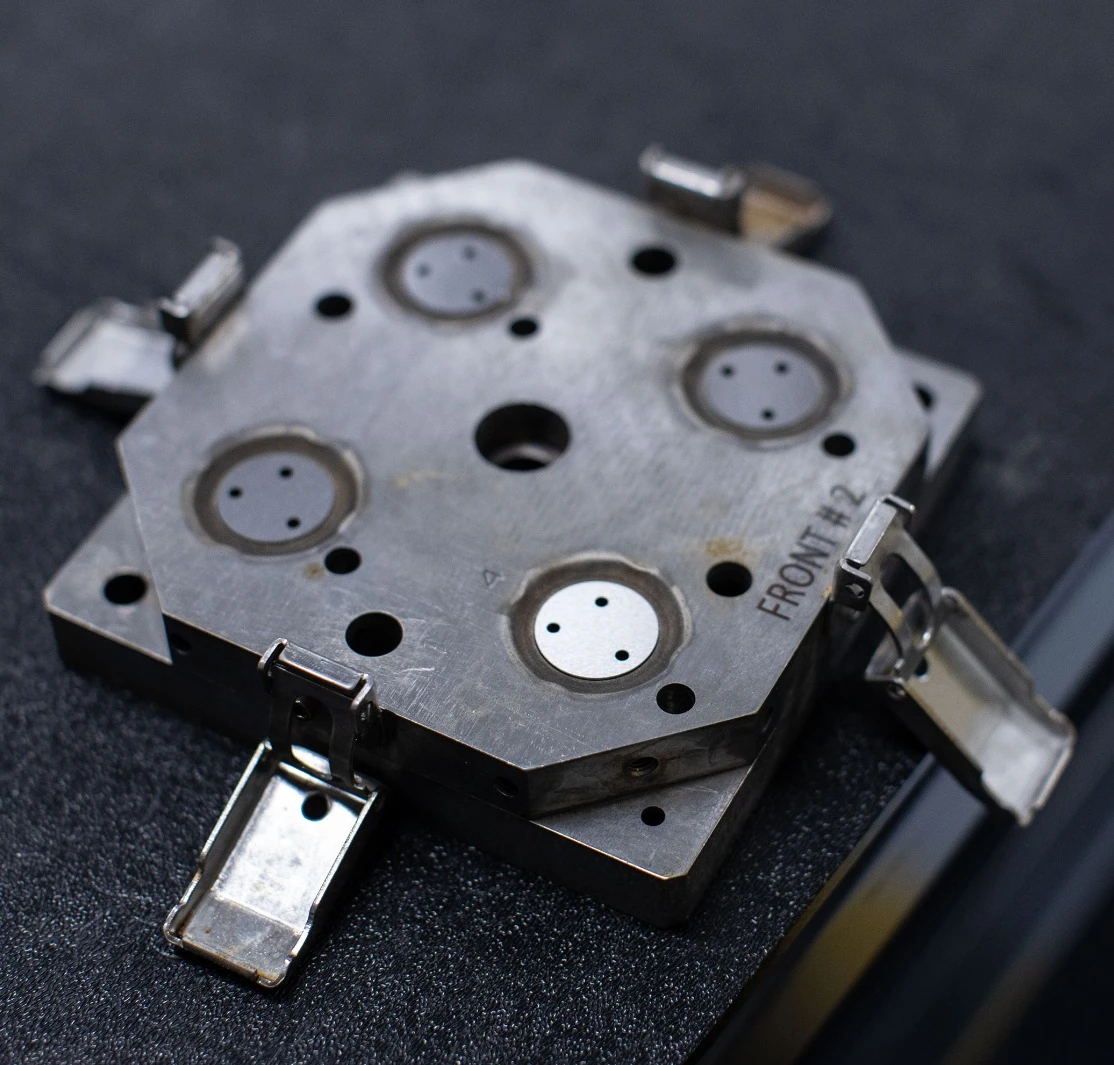