Machining Vs. Casting: Key Differences, Advantages, & Applications
When it comes to manufacturing metal parts, various methods can be used to create the same product. Although some of these processes can manufacture the same result, they utilize different techniques and technologies that each have their own advantages. Two of these manufacturing methods are CNC machining and die casting.
While both CNC machining and die casting can both create high-precision metal components with complex shapes, they’re each suited for different volumes, desired lead times, and more.
The article below will dive deeper into the differences between CNC machining and die casting, and help you decide when to use machining versus casting.
Defining Machining Vs. Casting
To understand the core differences between machining and casting, it’s important to start with what the two processes are.
What is CNC Machining?
CNC machining is a subtractive manufacturing process in which a machining tool forms a desired part based on computer-aided design (CAD) software. The tool uses a certain technique (drilling, cutting, hard milling, grinding, turning, and more) to remove material from a part to create the desired shape. CNC machining can work for high-strength materials like stainless steel, aluminum, and titanium to lighter-weight materials like plastics, acrylics, wood, and ceramics.
Learn more about how CNC machining can help manufacturing small metal parts in this article.
What is Die Casting?
Die casting, on the other hand, is a manufacturing process where molten metal is injected into a specifically designed mold. The material then cools and solidifies, at which point it’s removed from the mold and finished to create the desired part. Die casting can efficiently produce complex parts with intricate geometries, especially for larger quantities.
What are the Main Differences Between Machining and Casting?
So what makes these two methods unique? Here is an overview of their key differences, which we’ll elaborate on below.
|
|
|
Volume |
Ideal for lower volumes |
Ideal for higher volumes |
Materials |
Tougher materials |
Non-ferrous, lightweight materials |
Complexity of shapes |
Precise shapes with tight tolerances |
Ideal for complex internal cavities not possible with other methods, capable of complex designs |
Cost per part |
Typically higher |
Typically lower |
Lead Times |
Faster production, quicker turnaround times |
Longer overall process due to mold creation, fast production process thereafter |
Waste |
Typically more |
Typically less |
Surface finishing |
Excellent surface finishing |
Typically requires post-processing surface finishing to achieve same result as machining |
Volume
CNC Machining is better suited for lower-volume quantities because it’s a slower, more complex production process. Die casting is a faster production process (once the mold is created), so it works better for higher-volume projects compared to most CNC machining methods.
As a whole, machining can be a multi-step process where several different cutting techniques need to be performed one after the other, leading to slower overall production times. Casting is a singular operation, so it’s more efficient than CNC machining for higher-volume production.
Materials
While both methods can work with some of the same materials, machining often makes more sense for higher-strength metals and alloys like titanium.
Lighter-weight, non-ferrous (low iron composition) materials are usually more suitable for die casting, like aluminum, magnesium, and zinc. These materials usually have better fluidity and lower melting points, so they’re more easily injected and formed into the mold to create thin-walled components.
Want to learn more? Here’s a helpful material guide to die casting.
Complexity of Shapes
CNC machining can create complex shapes, but die casting actually has more capabilities in terms of geometries. Die casting can achieve air pockets and cavities that CNC machining can’t achieve in a single run – CNC machining may require additional runs to achieve the same result.
Cost
Unsurprisingly, longer production times typically result in higher cost per part for CNC machining. Labor, modern machines, and time can also spike machining costs. Casting’s ability to efficiently produce complex parts at higher quantities drives down cost per part, however it’s important to factor in the upfront cost of creating the mold itself.
Know that each method has exceptions that could make one more costly than the other. A manufacturer will be able to more accurately estimate a cost comparison.
Lead Times
Longer production times can lead to longer lead times for completed machined parts, and faster production during the casting process can make it more efficient than machining. However, the creation of the mold itself can take a while, which can increase lead times.
Waste
Being a subtractive manufacturing process, machining can often produce more waste compared to casting. Casting uses near-net shaping, meaning it requires minimal cutting, reducing the potential amount of waste.
Fortunately, depending on the material used, scrap may be recycled and reused for future projects.
Surface Finishing
Machining naturally results in a smoother surface finish as a result of the tool’s high precision, preventing the need for additional finishing. It’s common for die casting to require post-processing surface finishing to achieve the same high-quality finishing that CNC machining is able to produce.
Similarities Between Casting and Machining
You may have already noticed some similarities between casting and machining. For one, they can both produce complex shapes of a wide variety of materials. For example, both methods can produce components made of metals like aluminum, steel, iron or zinc.
Another significant similarity between the two are the industries and applications of their finished components. Both CNC machining and die casting are used to create high-strength components in the automotive, aerospace, medical and electronics industries.
Pros and Cons of Machining Vs. Casting
When choosing between one of these manufacturing methods, it’s helpful to consider the pros and cons of each. As you weigh the two, keep the following charts handy.
Machining
|
|
Ability to create complex shapes with intricate details and smooth finishes |
Lack of repeatability |
Ability to achieve tight tolerances |
Slow production speeds |
Suitability for a large range of materials |
Additional steps for different cuts required |
Efficiency |
Potential for more waste material |
Customization |
Casting
Pros |
Cons |
Ability to create cavities and other highly complex part designs |
Production speed slower than machining |
Repeatability |
Smaller range of material suitability compared to machining |
Cost-effectiveness for higher volume production |
Upfront cost of mold creation |
Suitability for a large range of materials |
Potential increase in lead times due to mold creation |
When to Use Casting Vs. Machining
So when should you use one method over the other? CNC machining is often more suitable for:
- Prototyping
- Low- to medium-volume projects
- Component design with no cavities or air pockets
- High-strength alloys
Die casting is often more suitable for:
- High-volume projects
- Extremely complex component shapes and designs
- Lighter-weight, non-ferrous materials
Closing Thoughts on Casting Vs. Machining
While CNC machining and die casting have a number of similarities, each manufacturing process is unique and better suited for certain materials and projects.
CNC machining can take longer and cost more upfront, but it’s compatible with a vast variety of materials and can achieve extremely tight tolerances on tough materials. The material compatibility for die casting may be limited, but it’s extremely efficient once the mold is created, and can accomplish cavity designs that CNC machining would require an additional run to achieve.
These are just two of many popular machining methods – visit our blog to learn about some of the innovative processes used each day in modern manufacturing.
You May Also Like
These Related Stories
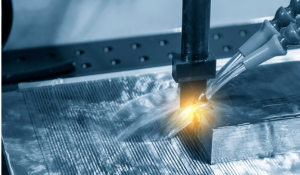
ECM Vs. EDM Machining: What’s the Difference?
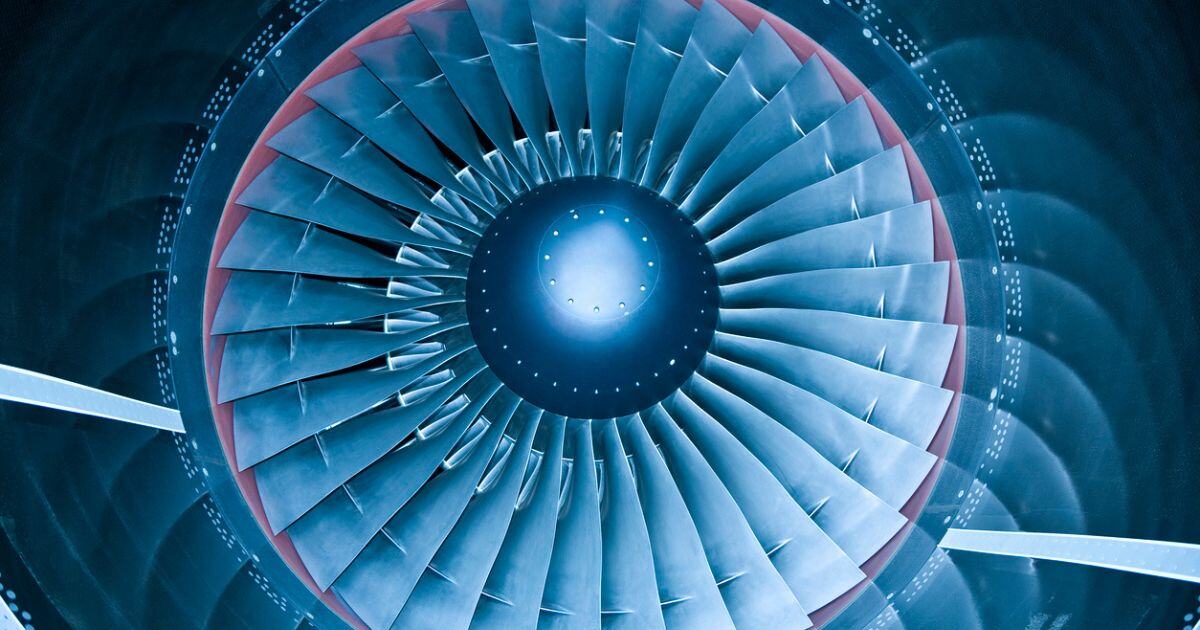
Using the Electrochemical Machining Process for the Aerospace Industry
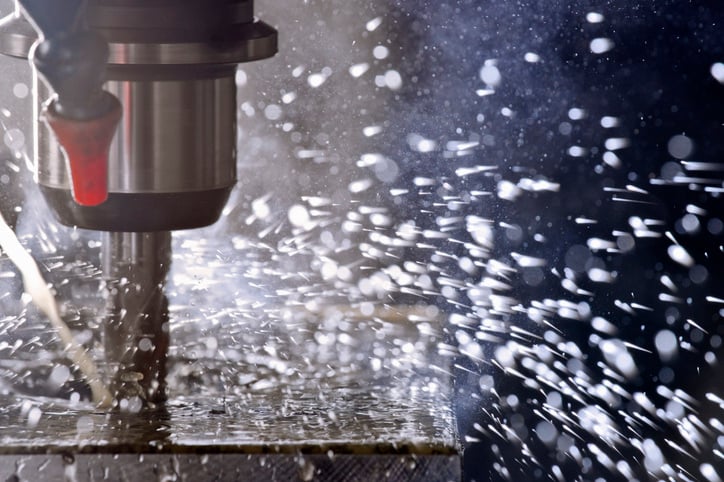