How Manufacturing Has Changed Over 50 Years: A Look at the History of Manufacturing with JV
Fifty years ago, manufacturing looked very different. Production floors were dominated by manual labor, machines were analog, and innovation often came slowly. Manufacturers relied heavily on generational know-how and hands-on craftsmanship, with little support from automation or digital systems.
Fast forward to today, and the transformation is undeniable. Technology, sustainability, and workforce evolution have redefined what it means to manufacture effectively. This shift hasn’t just changed how things are made – it’s elevated what customers can expect and how companies can deliver.
At JV Manufacturing, our journey began with a bold idea and the courage to innovate when others wouldn't. As we celebrate 50 years, we’re reflecting on how manufacturing has changed, and how we’ve grown right alongside it.
Then vs. Now: Key Shifts in Manufacturing
Over the last five decades, manufacturing has experienced some of the most significant changes in its history. What was once a process rooted in manual tools and generational knowledge has evolved into a sophisticated, tech-driven industry thriving on innovation, speed, and precision.
JV Manufacturing has lived and led through these changes. By staying adaptable and investing in the right tools, people, and values, we’ve not only kept pace with the industry, we’ve helped push it forward. Here’s a look at some of the biggest transformations we’ve seen, and how JV has evolved alongside them.
Technology & Automation
Then: Fifty years ago, die stamping operations were highly manual. Presses were mechanically driven, and tooling setups required hands-on adjustments. Processes like progressive die stamping were less common or far less automated, and most production relied on single-station stamping setups. Tool and die teams needed deep mechanical intuition to make parts fit and function properly. At JV, early work was done on analog presses with carefully machined dies, shaped and maintained by experienced craftsmen using traditional techniques.
Now: Today, JV Manufacturing uses cutting-edge CNC machining, robotics, and AI-supported systems to produce high-quality metal stampings with greater speed and precision than ever before. These manufacturing technology changes have reshaped how we work, and we’ve embraced them at every stage, expanding our capabilities and solving complex challenges that others couldn’t crack. Whether it’s stamping intricate logos without distortion or developing tools for challenging parts, technology helps us deliver solutions with confidence.
Workforce & Skills
Then: The manufacturing workforce in the 1970s was largely composed of skilled tradespeople – tool and die makers, press operators, machinists – who learned their craft over years of hands-on experience. Much knowledge was passed down informally, often through mentoring or on-the-job training. The work was physical, precise, and required a deep understanding of materials and machinery. At JV, the earliest teams were small, tight-knit, and relied on each other’s grit and ingenuity to get the job done.
Now: While digital tools and automation have become essential in modern manufacturing, the value of experience and craftsmanship remains just as strong. At JV, we blend time-tested skill with modern capabilities. Roles like tool and die maker are still vital, requiring deep knowledge and precision – even as the tools they use have become more advanced.
We’ve invested in developing our people, prioritizing training, mentorship, and cross-disciplinary collaboration. At the leadership level, we’ve embraced a more transparent, people-first culture that empowers employees to contribute their voices and ideas.
Materials & Product Innovation
Then: In the early days, manufacturers typically worked with standard materials like cold-rolled steel, aluminum, and basic composites. These materials were widely available, cost-effective, and suitable for the straightforward designs of the time. However, options for customization or enhanced performance were limited. Product development cycles were longer, and most customers focused on function over form.
Now: Today, advanced alloys, sustainable materials, and custom-engineered solutions drive product innovation. JV Manufacturing has responded by expanding our expertise and investing in process improvements, allowing us to work with a wider range of materials and meet increasingly complex specs. Innovation isn’t a buzzword here, it’s the reason we’ve been able to grow, solve tough customer problems, and remain a trusted partner.
Sustainability & Efficiency
Then: Decades ago, environmental awareness wasn’t a major factor in manufacturing. Efficiency focused more on output and less on minimizing resource use or optimizing energy consumption. Lean manufacturing had not yet become a widespread practice. Priority was delivering durable parts at scale, and sustainability would emerge as a strategic focus much later.
Now: JV Manufacturing has taken steps to reduce waste, improve energy use, and invest in lean manufacturing principles. From in-house initiatives to community involvement, our commitment to sustainability reflects our values and our responsibility to future generations.
Customer Expectations & Market Demands
Then: Customers typically wanted large-volume production runs of standard parts. Lead times were longer and there was less expectation for speed, customization, or design input. Communication was handled through phone calls or printed drawings, and change requests often slowed down the process. Flexibility and responsiveness were limited by the slower pace of the era’s manufacturing tools and processes.
Now: Today’s customers demand flexibility, customization, and real-time communication. JV has responded by becoming more agile and responsive than ever. Whether it’s adapting a tool for a last-minute deadline or stepping in when other suppliers fall short, we’re known for going the extra mile and doing it quickly.
A Look Back: Milestones from Our Journey
Over the decades, we’ve grown significantly, from our original location in 1975 to the opening of our second facility at 10 Acee Drive, a milestone that expanded our capacity and opened the door to future opportunities. We’ve continuously invested in new equipment, expanded our workforce, and built lasting relationships with customers across industries.
As a family-owned manufacturing company, family has always been central to our journey. Ryan Vecchi recalls growing up around the company and JV still hosts the same family-oriented events, like picnics and celebrations, that once brought him joy as a kid. Whether it’s handwritten thank-you notes, baby showers for employees, or helping customers meet impossible deadlines, our culture reflects the care and commitment of a true family business.
Where We’re Headed: The Future of Manufacturing
Looking ahead, we’re excited about what’s next. The future of manufacturing lies in smart manufacturing trends like AI, IoT, and data-driven optimization – and we’re ready.
We’re expanding our services, exploring new technology, and continuously growing our team’s capabilities to meet the evolving needs of our customers. A third facility may be on the horizon, and we’re committed to staying at the forefront of innovation.
We also recognize the importance of representation and diversity. Our support of Women in Manufacturing and similar initiatives shows our dedication to building a more inclusive, dynamic industry for the future.
50 Years Strong — and Just Getting Started
A lot has changed in 50 years, but our core values remain the same. We’re still driven by innovation, guided by relationships, and proud of the quality we deliver every day. As we celebrate this milestone, we’re honoring our past and embracing our future, with gratitude for the people, partners, and customers who’ve helped shape our story.
Follow us on social media to stay connected as we begin our next chapter!
You May Also Like
These Related Stories
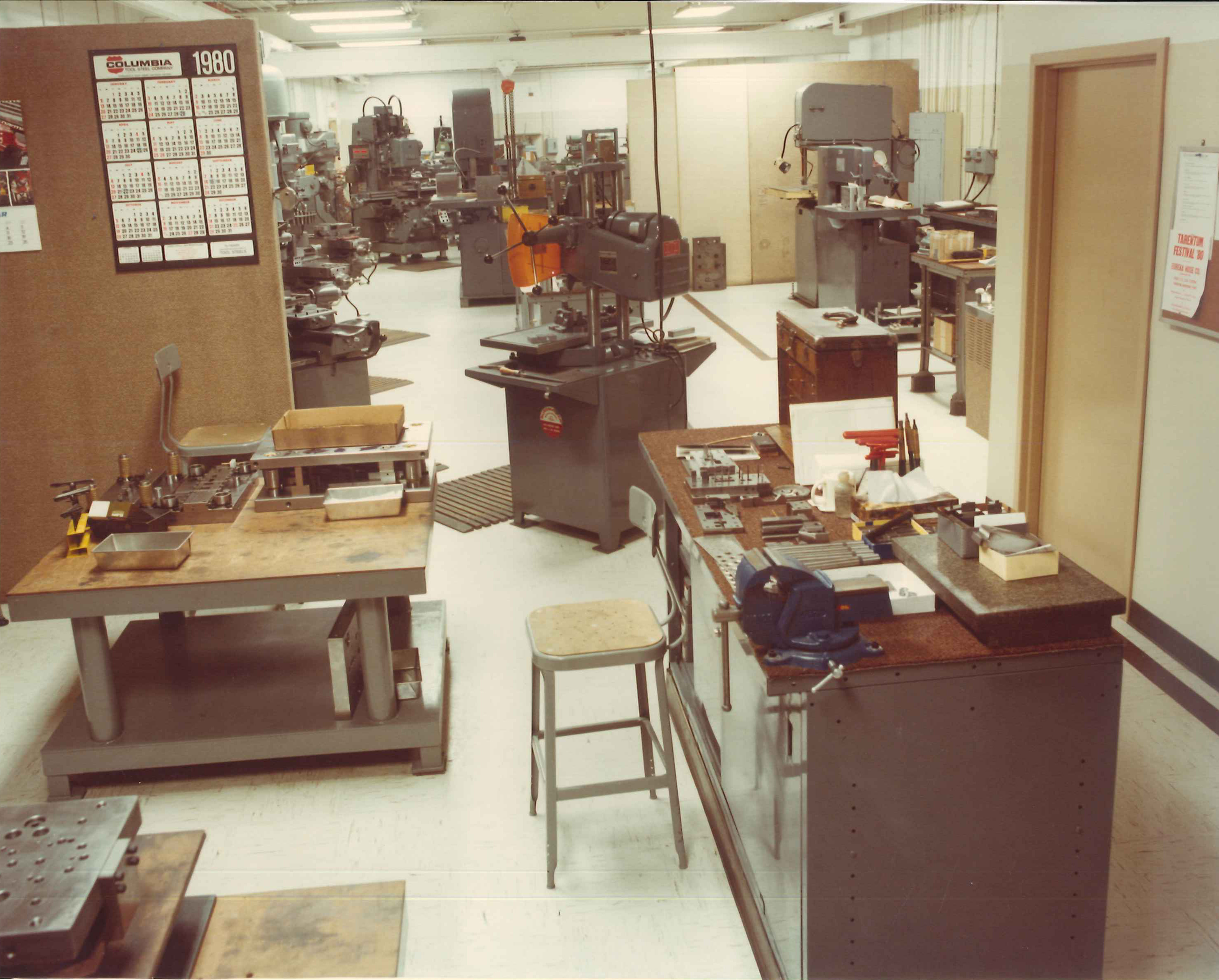
Meet JV Manufacturing: Stories from Our Longest-Serving Employees
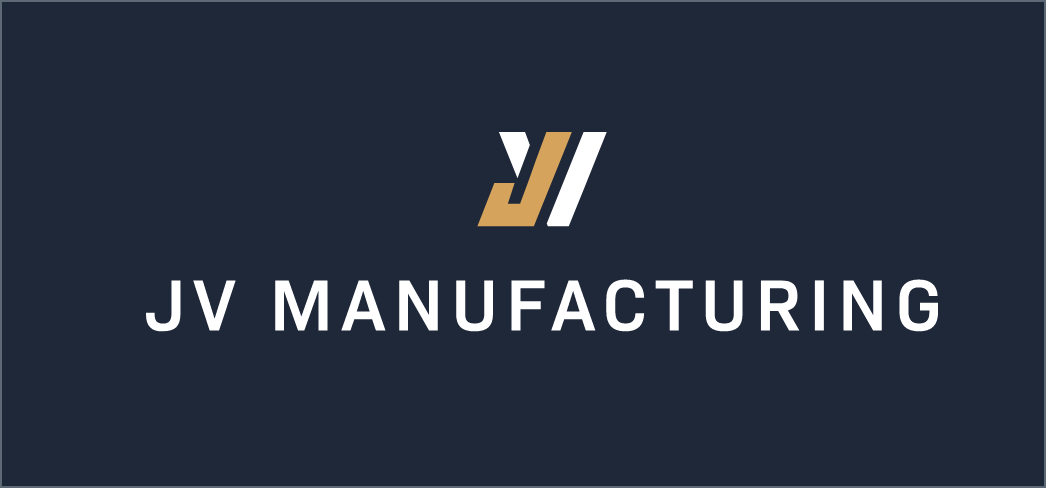
A Manufacturing Family 45 Years in the Making
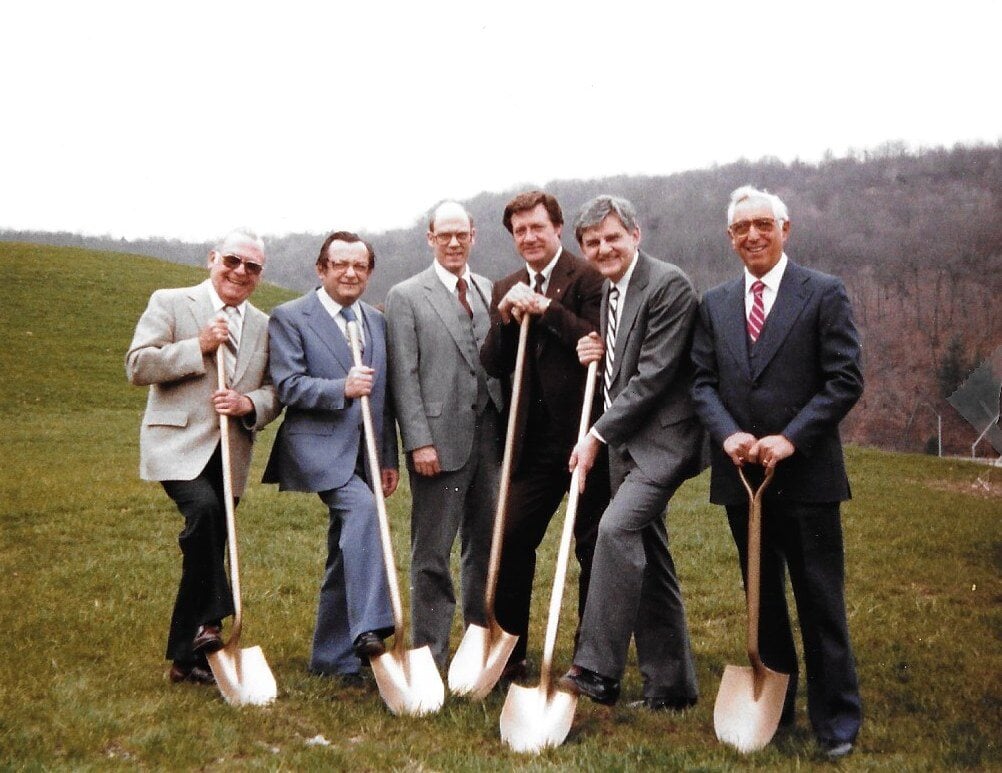